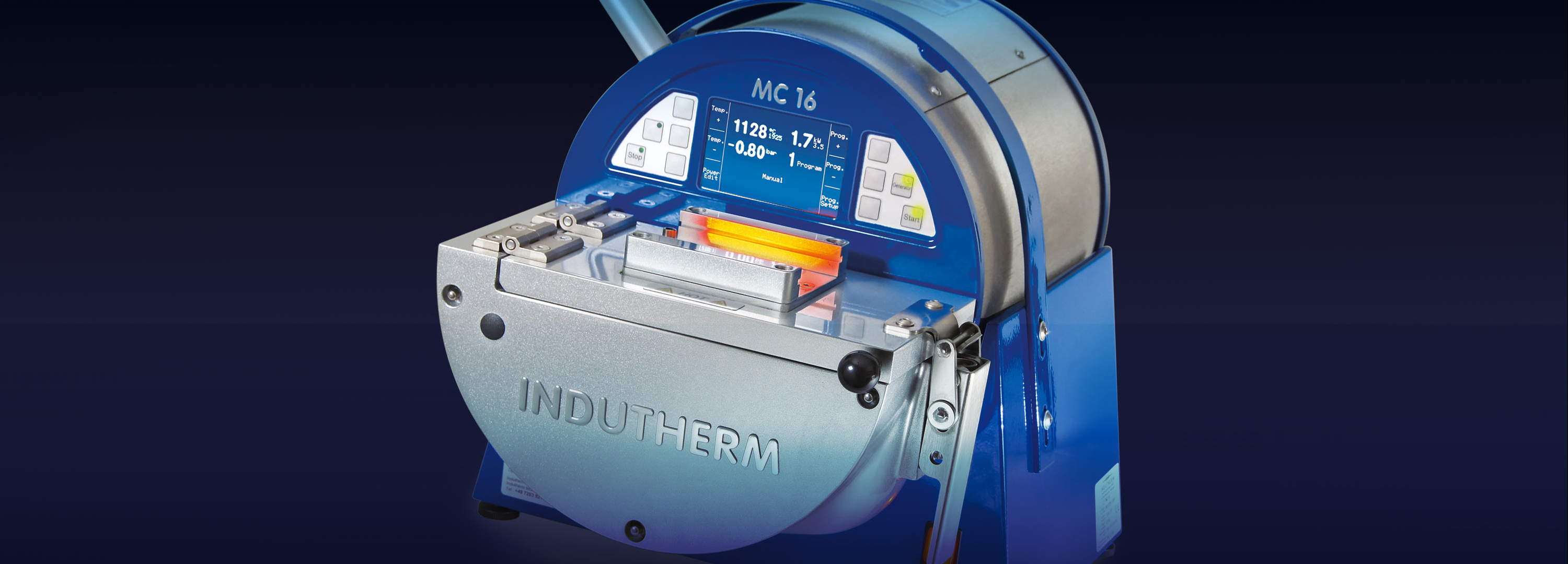
From model to casting within 1 hour!
The compact MC series was developed to provide jewellery designers, goldsmiths, development departments and dental laboratories with a cheap yet highly professional casting machine. Our most important aims were: extremely short processing time from mould manufacturing to completed casting; simple, safe operation; high quality and, above all, reproducible casting results; and low operating costs. The overwhelming global success of the MC series in numerous industries – including some not originally envisaged – emphatically confirms the MC concept
For even more than just for lost wax casting
The MC series machines are also used
- for analytic purposes where material samples needs to be molten down, homogenized and cast into a defined shape (also possible for powder)
- for the production of small quantities of cast semifinished material like rods or sheet
Ingeniously simple = simply ingenious
With the MC machines, you can easily cast by hand from the crucible to your mould and feel what you are doing – just as it has been done for thousands of years. So that this works consistently and safely, the entire melting/ casting unit is tilted together through a 90° angle. For perfect balance and to make do with as few moving parts as possible, almost the whole machine moves during tilting: being cylindrical in design, the whole moving section rotates as if in a halfpipe – ingeniously simple and stylishly designed on high-quality rollers. However, unlike manual casting, the process takes place in an enclosed chamber under a vacuum or inert gas atmosphere, to prevent air pockets and oxidation. You can check the melting and pouring-off process through the sight glass.
Full text LCD display for fine adjustment and serial programming
The new operating system features individual setting of parameters to achieve maximum performance from every pattern mould and every alloy. Thanks to the transparent layout of the menu structure and full text display, all settings are quick and easy to program. Of course all process parameters can be saved for repeated castings.
Vibration technology for excellent casting quality
The MC machines with the “V” suffix are equipped with the Indutherm vibration system (see page 20). Vibration switched on directly after casting is a decisive factor in enhancing mould filling with very filigree parts. It prevents porosity, ensures a finer grain structure and allows greater and more constant density. Parts have measurably higher elasticity and this increases the scope for further processing significantly. Vibration technology is a compelling alternative to the frequently used and relatively delicate centrifugal systems, especially when casting platinum or palladium.
Handling the mini casting system is extremely simple:
- Fill in the material and heat up
- Define your considered process parameters e.g. atmosphere: vacuum, inert gas atmosphere, overpressure
- Take the mold from oven and insert into the machine. The device itself looks after all additional functions – until we get to the stroke of genius:
- Pouring off takes place using a 90° rotation of the casting unit. After pouring, the MC machine automatically switches to overpressure in order to optimise the mould filling even for delicate parts
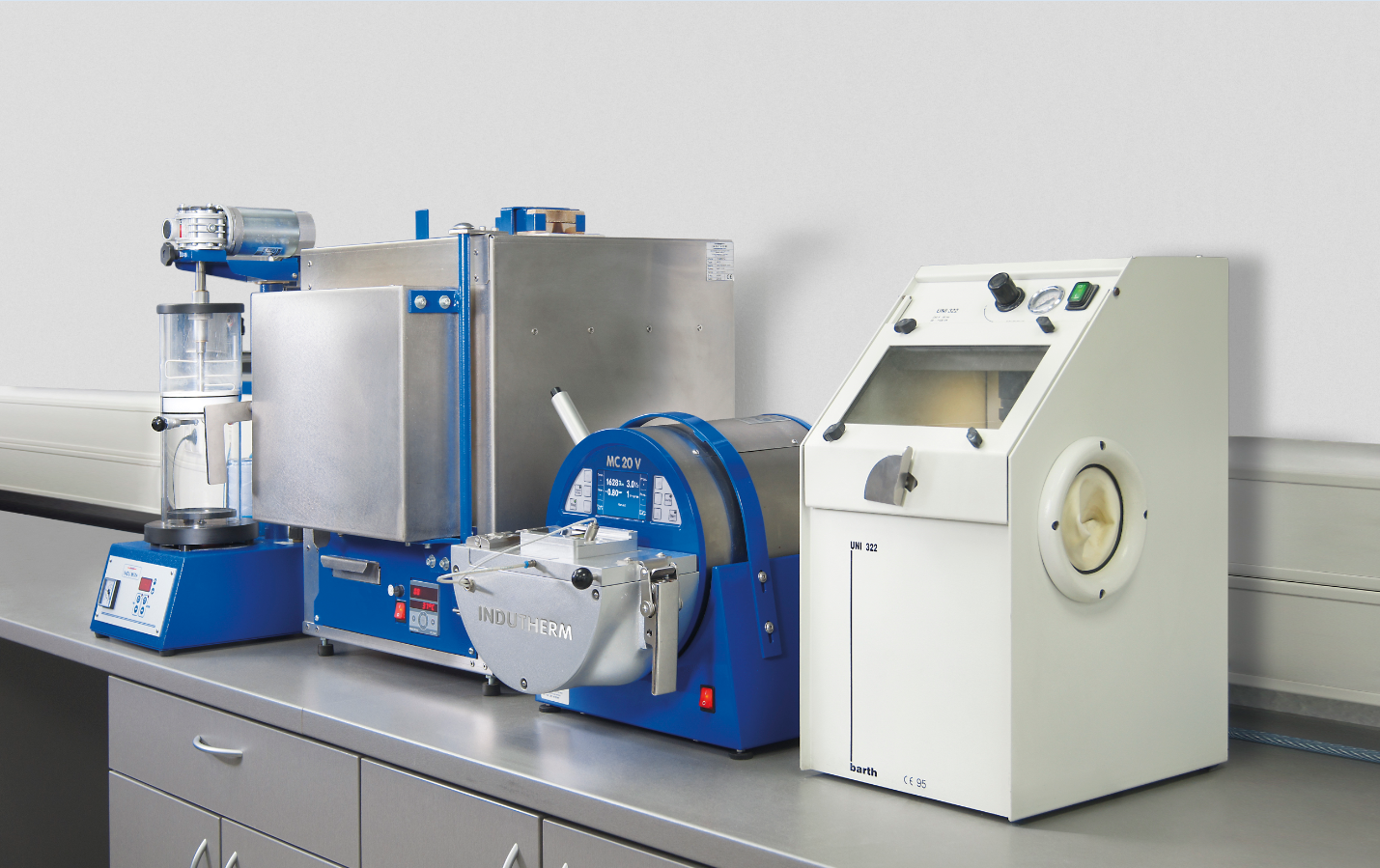
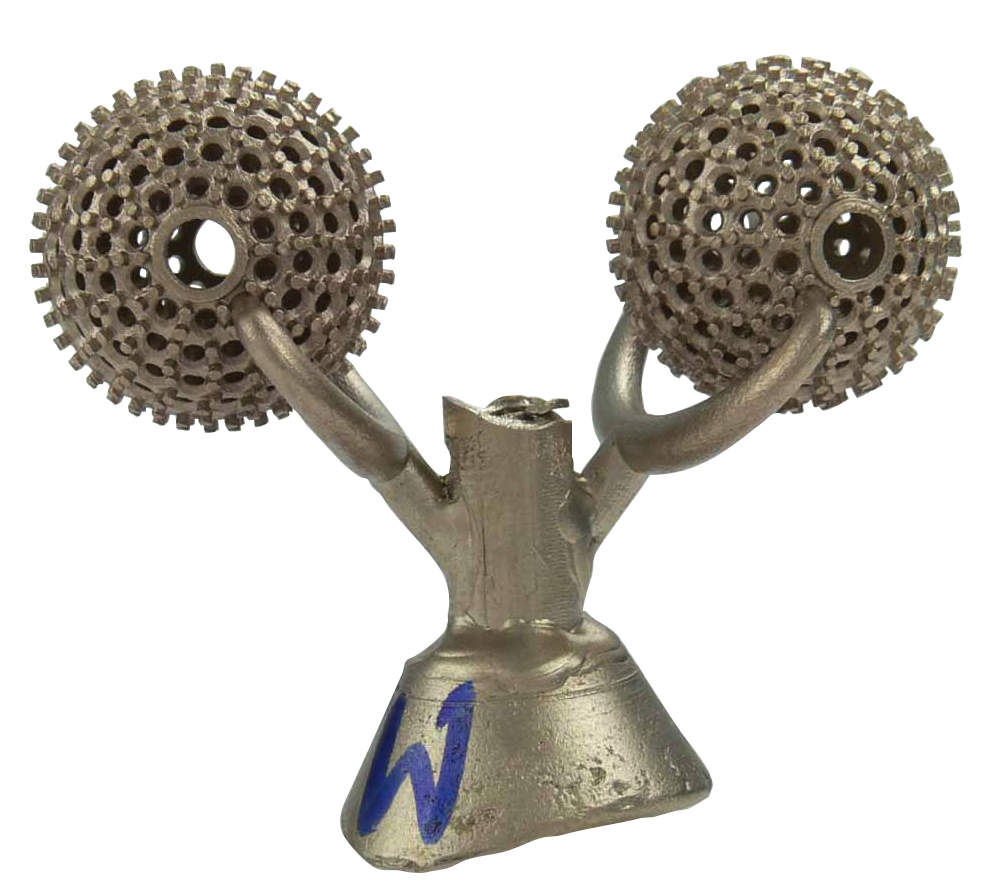
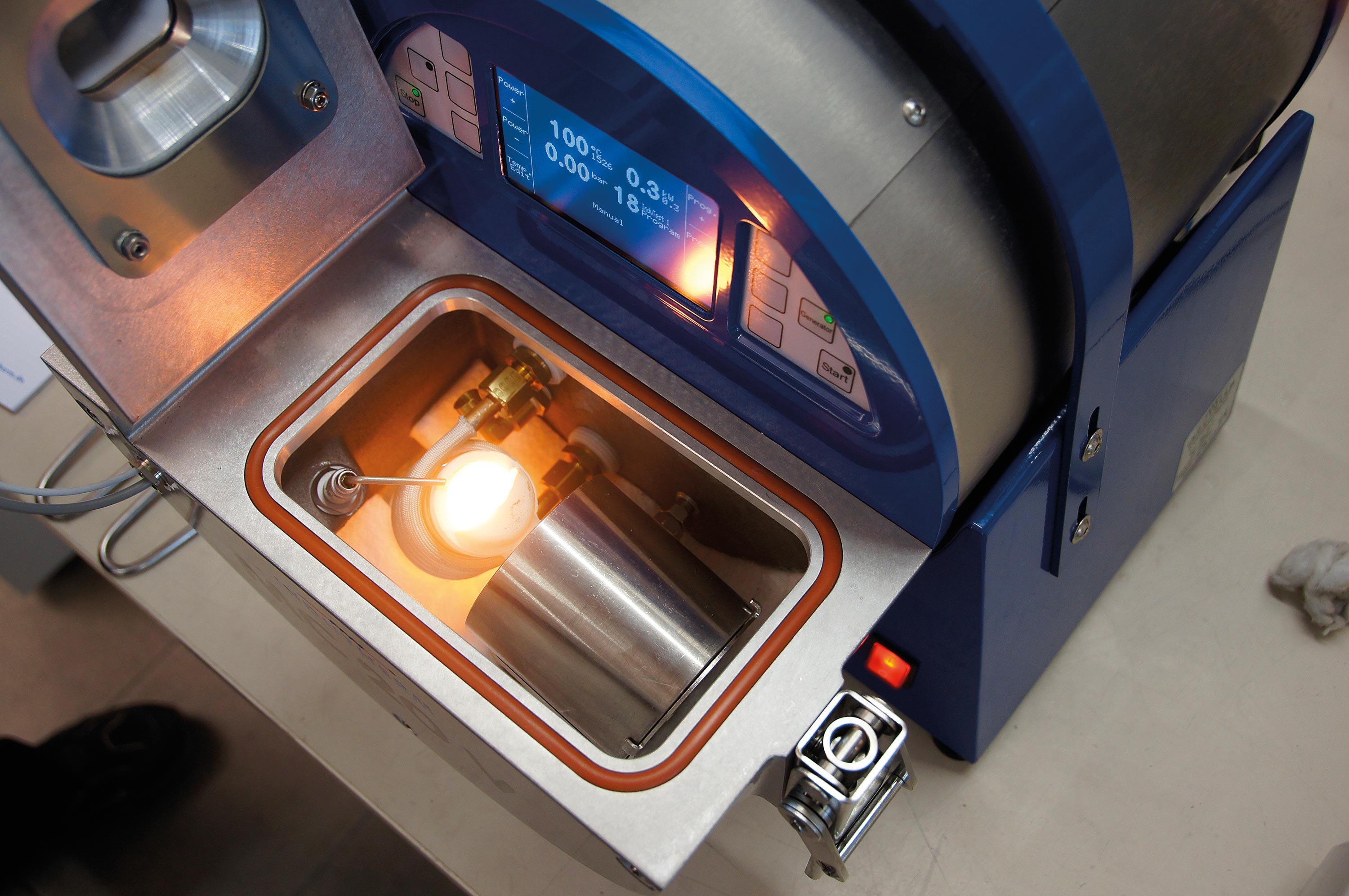
Data Overview of MC-Series
■ standard equipment, ○ optional, - not availableMC 16 | MC 20 V | MC 60 V | MC 100 V | MTC 100 V | |
Power
|
|||||
Power max. / electrical connection | 3,5 kW (230v single phase) | 3,5 kW (230v single phase) | 3,5 kW (230v single phase) | 8 kW (3x400v) | 8 kW (3x400 V) |
Temperature max. | 2000° C | 2000° C | 1300° C | 2000° C | 2100° C |
Capacity
|
|||||
Crucible Volume | 100g Au 18 ct 110g steel 200g Pl | 100g Au 18 ct 110g steel 200g Pl | 450g Au 18 ct 300g Ag 935 |
450g Au 18 ct 250g steel 500g Pl | 450g Au 18 ct 250g steel 500g Pl |
Volume ceramic crucible | 30 ccm = 600 g Pt / 250 g steel | ||||
For use of molds | up to ø 30/50/65/80 mm x 80 mm h | up to ø 30/50/65/80 mm x 80 mm h | up to ø 80/100 mm x 120 mm h | up to ø 80/100 mm x 120 mm h | bis ø 100 mm x 150 mm H |
Volume graphite crucible | 25 ccm = 450 g Au 18 ct | ||||
Operation and Control
|
|||||
Control system | by LCD-display, full text readout | by LCD-display, full text readout | by LCD-display, full text readout | by LCD-display, full text readout | by LCD-display, full text readout |
Maximum pressure | 3 bar | ||||
Turbo Pressure PLUS system | ■ | ||||
Automatic vacuum function | ■ | ■ | ■ | ■ | ■ |
Automatic overpressure function | ■ | ■ | ■ | ■ | ■ |
Casting also under vacuum only | ■ | ■ | ■ | ■ | |
Vacuum/Inert gas overpressure | ■ | ||||
Vacuum or overpressure after casting | –1 up to +2 bar | –1 up to +3 bar | –1 up to +2 bar | –1 up to +3 bar | –1 up to +3 bar |
Function washing by inert gas | ■ | ■ | ■ | ■ | ■ |
Temp. measurement by thermocouple | ■, up to 1.300° C | ||||
Vibration system | - | ■ | ■ | ■ | ■ |
Supply: cooling water, inert gas argon or nitrogen | ■ | ■ | ■ | ■ | ■ |
Temperature measurement/control | ■ up to 1.300° C, ○ up to 1.600° C | ■ up to 2000° C | ■ up to 1300° C | ■ up to 2000° C | ■ bis 2100° C |
Temperature measurement equipped with an optical pyrometer | - | ■ | - | ■ | up to 2000° C |
Temperature measurement equipped with a dual wave pyrometer | - | ○ | - | ○ | ○ |
Quality Assurance
|
|||||
RS 232, Ethernet, USB interface, diagnostic system | ■ | ■ | ■ | ■ | ■ |
GSM-modem for remote service | ○ | ○ | ○ | ○ | ○ |
DMS
|
■ | ■ | ■ | ■ | ■ |
InduthermCloud | ○ | ○ | ○ | ○ | ○ |
iThermControl | ○ | ○ | ○ | ○ | ○ |
Accesories
|
|||||
Vacuum investment mixer Indumix 2+ | ○ | ○ | ○ | ○ | ○ |
Vacuum investment mixer Indumix 3+ | ○ | ○ | ○ | ○ | ○ |
Furnace AK 20 | ○ | ○ | ○ | ○ | ○ |
Furnace AK 50 | ○ | ○ | ○ | ○ | ○ |
Sand blasting cabinet | ○ | ○ | ○ | ○ | ○ |
Vacuum pump up to 8 m³ /h | ○ | ○ | ○ | ○ | ○ |
Vacuum pump up to 21 m³ /h | - | - | ○ | ○ | - |
Vacuum pump | ○ | ||||
Floor unit | - | - | - | ○ | - |
Water chiller | ○ | ○ | ○ | ○ | ○ |
Other Advantages of MC-Series
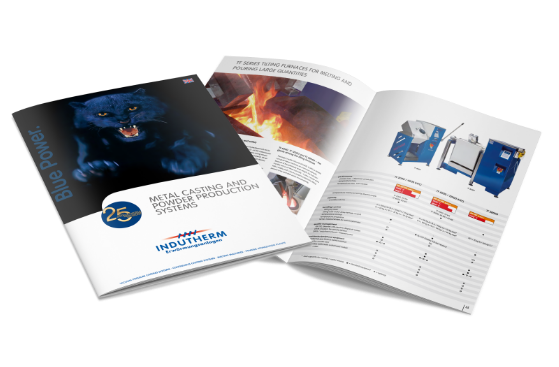