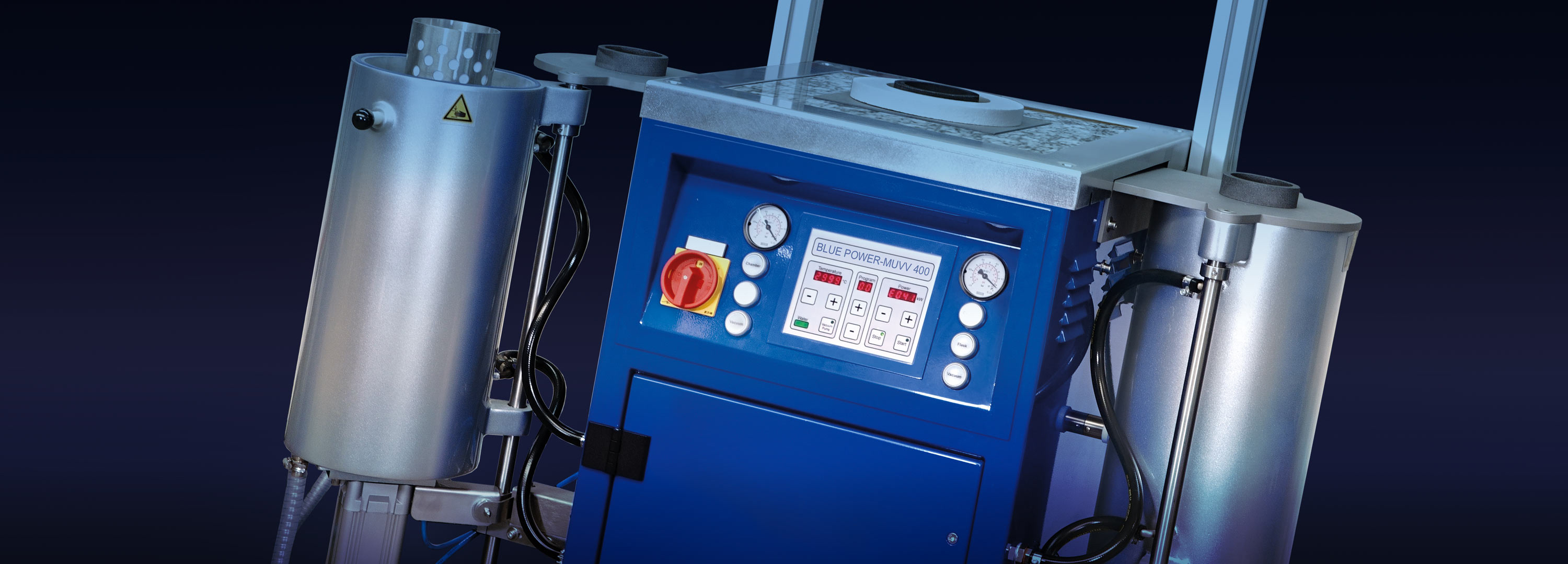
With the MU series we offer melting machines for many different demands and with crucible capacities from 155 ccm up to 1,200 ccm. The material is molten in open crucibles and poured by hand into the mould.
Melting Units MU Series
Flexible melting furnaces designed to melt gold and silver alloys and as well as aluminium, bronze, brass a.s.o. Due to the strong induction generator up to 15 kW and the low induction frequency the stirring effect of the metal is excellent.
The MU as vacuum casting machine
The V-versions include one or two additional extra large capacity vacuum chambers. The evacuation of the flask immediately after pouring improves the form filling, reduces porosity and avoids the oxidisation of the hot metal.
The MU melting systems are also available as high-temperature melting systems with ceramic crucibles.
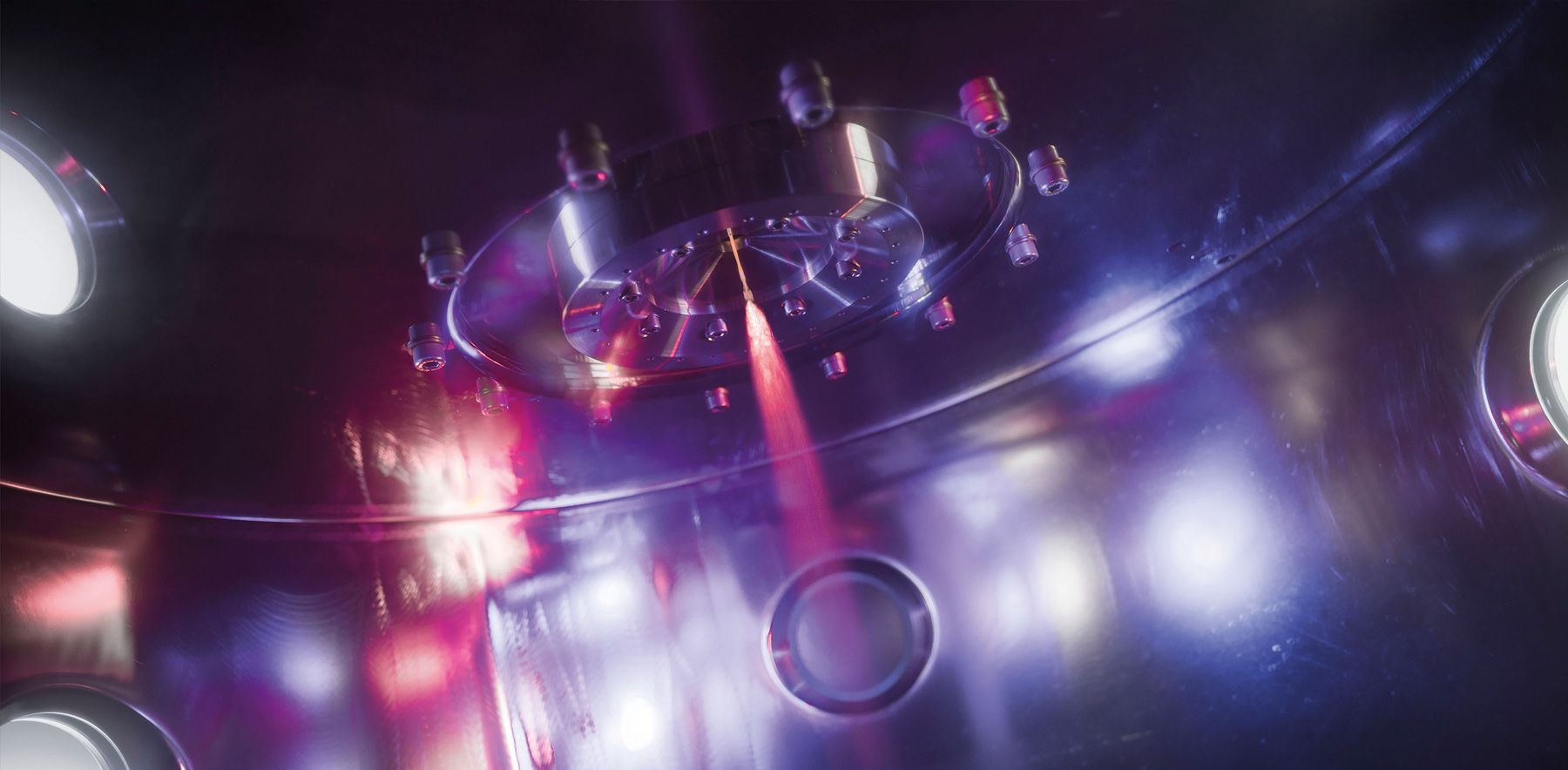
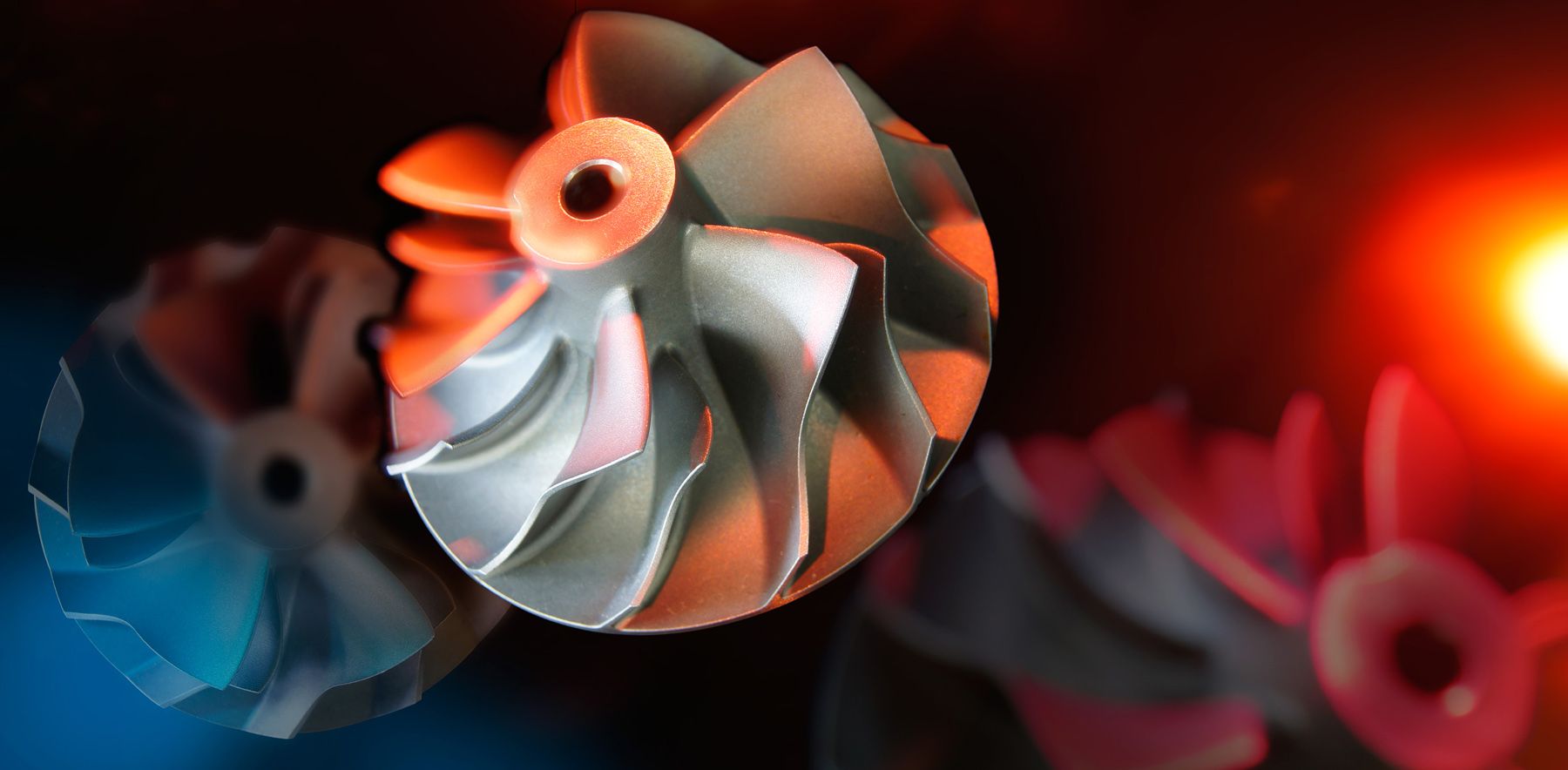
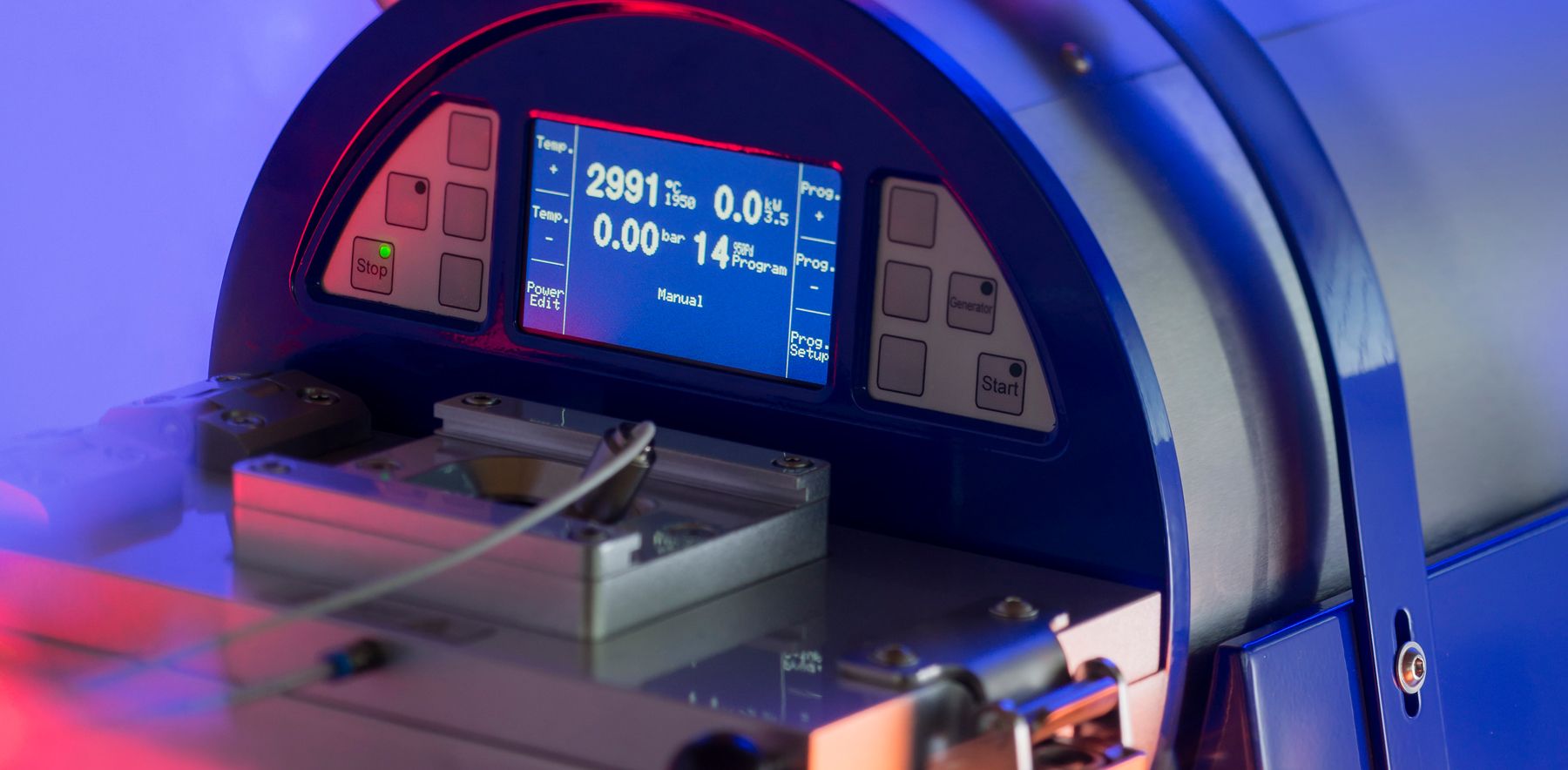
Data Overview of MU-Series
■ standard equipment, ○ optional, - not availableMU-Series | MU-Series | MU-Series | MU-Series | MU-Series | MU-Series | MU-Series | MU-Series | MU-Series | MU-Series | MU-Series | MU-Series | MU-Series | MU-Series | MU-Series | MU-Series | MU-Series | MU-Series | |
Power
|
||||||||||||||||||
Power max. / electrical connection | 3.5 kW (230 V)|6 kW (3x400 V) | 3.5 kW (230 V)|6 kW (3x400 V) | 3.5 kW (230 V)|6 kW (3x400 V) | 10 kW (3x400 V) | 10 kW (3x400 V) | 10 kW (3x400 V) | 12 kW (3x400 V) | 12 kW (3x400 V) | 12 kW (3x400 V) | 15 kW (3x400 V) | 15 kW (3x400 V) | 15 kW (3x400 V) | 15 kW (3x400 V) | 15 kW (3x400 V) | 15 kW (3x400 V) | 12 kW (3x400 V) | 12 kW (3x400 V) | 12 kW (3x400 V) |
Capacity
|
||||||||||||||||||
Crucible Volume | 155 ccm = 2,0 kg Au 18ct / 1,2 kg Cu * | 155 ccm = 2,0 kg Au 18ct / 1,2 kg Cu * | 155 ccm = 2,0 kg Au 18ct / 1,2 kg Cu * | 400 ccm** = 5,0 kg Au 18ct/3,2 kg Cu* | 400 ccm** = 5,0 kg Au 18ct/3,2 kg Cu* | 400 ccm** = 5,0 kg Au 18ct/3,2 kg Cu* | 700 ccm** = 8,5 kg Au 18ct/5,5 kg Cu* | 700 ccm** = 8,5 kg Au 18ct/5,5 kg Cu* | 700 ccm** = 8,5 kg Au 18ct/5,5 kg Cu* | 900 ccm** = 11,0 kg Au 18ct/7,2 Kg Cu* | 900 ccm** = 11,0 kg Au 18ct/7,2 Kg Cu* | 900 ccm** = 11,0 kg Au 18ct/7,2 Kg Cu* | 1200 ccm** = 14,5 kg Au 18ct/10,0 kg Cu* | 1200 ccm** = 14,5 kg Au 18ct/10,0 kg Cu* | 1200 ccm** = 14,5 kg Au 18ct/10,0 kg Cu* | 155 ccm = 2,5 kg Pt / 1 kg steel * | 155 ccm = 2,5 kg Pt / 1 kg steel * | 155 ccm = 2,5 kg Pt / 1 kg steel * |
(Non-)Perforated molds without flange | - | up to ø 400 mm h | up to ø 400 mm h | - | up to ø 400 mm h | up to ø 400 mm h | - | up to ø 400 mm h | up to ø 400 mm h | - | up to ø 400 mm h | up to ø 400 mm h | - | up to ø 400 mm h | up to ø 400 mm h | - | ø 400 mm h | ø 400 mm h |
(Non-)Perforated molds with flange | - | up to ø 160 mm h | up to ø 160 mm h | - | up to ø 160 mm h | up to ø 160 mm h | - | up to ø 160 mm h | up to ø 160 mm h | - | up to ø 160 mm h | up to ø 160 mm h | - | up to ø 160 mm h | up to ø 160 mm h | - | ø 160 mm h | ø 160 mm h |
Operation and Control
|
||||||||||||||||||
Programs | 20 | 20 | 20 | 20 | 20 | 20 | 20 | 20 | 20 | 20 | 20 | 20 | 20 | 20 | 20 | - | - | - |
Temperature control | ■ | ■ | ■ | ■ | ■ | ■ | ■ | ■ | ■ | ■ | ■ | ■ | ■ | ■ | ■ | ■ | ■ | ■ |
Temp. measurement by thermocouple | ■ | ■ | ■ | ■ | ■ | ■ | ■ | ■ | ■ | ■ | ■ | ■ | ■ | ■ | ■ | - | - | - |
Temp. measurement by optical pyrometer | 1300° C|1500° C | 1300° C|1500° C | 1300° C|1500° C | 1500° C|1850° C** | 1500° C|1850° C** | 1500° C|1850° C** | 1500° C|1850° C** | 1500° C|1850° C** | 1500° C|1850° C** | 1500° C|1850° C** | 1500° C|1850° C** | 1500° C|1850° C** | 1500° C|1850° C** | 1500° C|1850° C** | 1500° C|1850° C** | 2000° C | 2000° C | 2000° C |
Temperature measurement equipped with an optical pyrometer | ○ | ○ | ○ | ○ | ○ | ○ | ○ | ○ | ○ | ○ | ○ | ○ | ○ | ○ | ○ | ○ | ○ | ○ |
Quality Assurance
|
||||||||||||||||||
RS 232, Ethernet, USB interface, diagnostic system | - | - | - | - | - | - | - | - | - | - | - | - | - | - | - | - | - | - |
Diagnostic system | ■ | ■ | ■ | ■ | ■ | ■ | ■ | ■ | ■ | ■ | ■ | ■ | ■ | ■ | ■ | ■ | ■ | ■ |
GSM-modem for remote service | ○ | ○ | ○ | ○ | ○ | ○ | ○ | ○ | ○ | ○ | ○ | ○ | ○ | ○ | ○ | ○ | ○ | ○ |
DMS
|
■ | ■ | ■ | ■ | ■ | ■ | ■ | ■ | ■ | ■ | ■ | ■ | ■ | ■ | ■ | ■ | ■ | ■ |
InduthermCloud | ○ | ○ | ○ | ○ | ○ | ○ | ○ | ○ | ○ | ○ | ○ | ○ | ○ | ○ | ○ | ○ | ○ | ○ |
iThermControl | ○ | ○ | ○ | ○ | ○ | ○ | ○ | ○ | ○ | ○ | ○ | ○ | ○ | ○ | ○ | ○ | ○ | ○ |
Accesories
|
||||||||||||||||||
Vacuum pump | ○ | ○ | ○ | ○ | ○ | ○ | ○ | ○ | ○ | ○ | ○ | ○ | ○ | ○ | ○ | ○ | ○ | ○ |
Water chiller | ○ | ○ | ○ | ○ | ○ | ○ | ○ | ○ | ○ | ○ | ○ | ○ | ○ | ○ | ○ | ○ | ○ | ○ |
* real capacity for casting / useful volume
** high temperature versions with reduced crucible volume
All machine descriptions and technical data published on this site make no claim to be complete. They are subject to change and therefore they are not basis of contract.
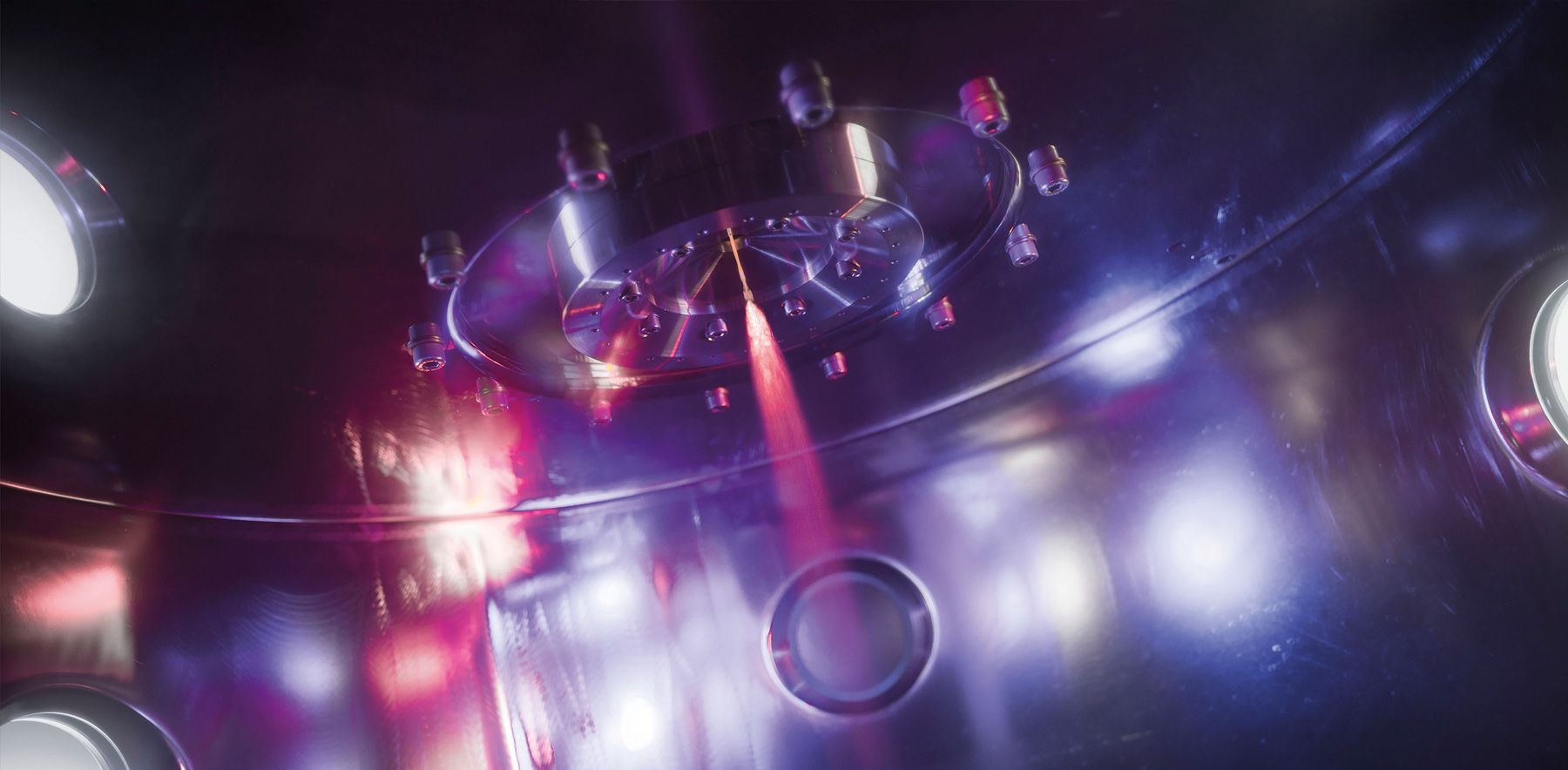
Find more about MU-Series
MU-Series-Systems in the recycling process
With the MU and MUV series we offer melting systems for a wide range of requirements Crucible capacities from 155 cc to 1,200 cc. The material is melted in open crucibles and from hand in the Casting mold or chill.
Melting systems MU-Serie
These melting furnaces are used to melt gold and silver alloys as well as aluminum, bronze and Brass. Due to the strong induction generator (up to 15 kW) and the low induction frequency, the Mixing of the metal is excellent.
MU as a vacuum casting system:
The MUV/MUVV series The V versions are equipped with one or two additional vacuum chambers big Capacity equipped. Evacuating the mold immediately after casting improves this mold filling, reduces porosity and avoids oxidation of the hot metal.
The high-temperature melting system MU 200 C
With its direct inductive heating system, the MU 200 C is suitable for melting metals at high temperatures melting point How Steel, palladium, platinum, chrome-cobalt, etc. are ideal.
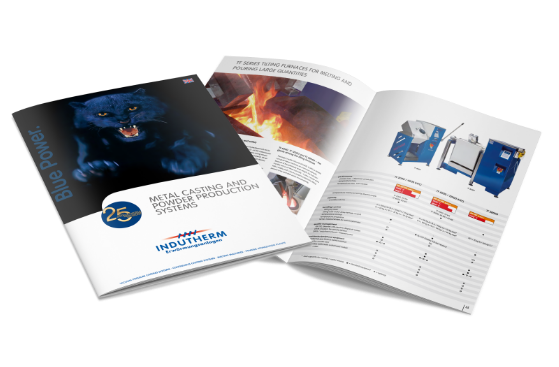