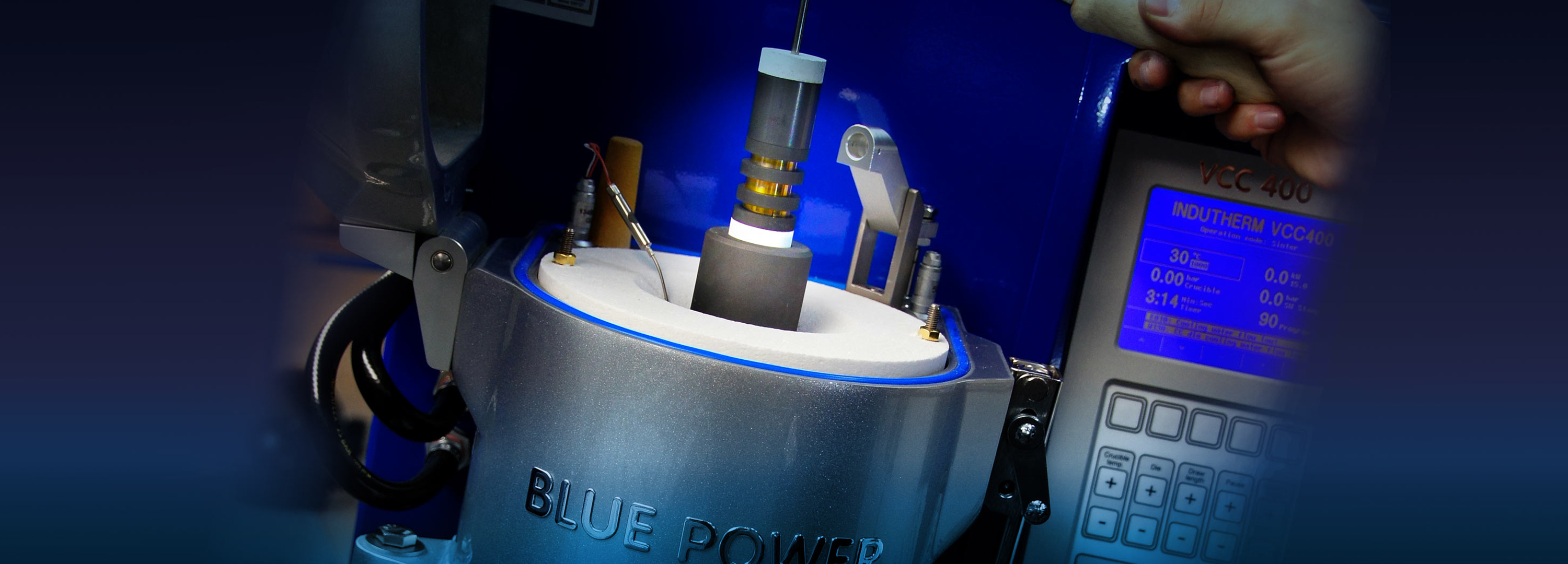
Sintering / diffusion welding
Diffusion welding (often called „sintering”), is the optimal process for producing multicolor rings. Metals are processed under pressure and at temperatures just below the solidification point. The pressure is generated pneumatically and not mechanically via a threaded spindle. This prevents the graphite elements used from breaking when they expand due to heat. The connecting layer has the same resilience as the metal itself. Expanding and reducing finished wedding rings is easily possible over a very large area (7 sizes and more).
Indutherm offers various options for diffusion welding:
The sinter kit for converting existing casting systems or special sintering systems, the SU series.
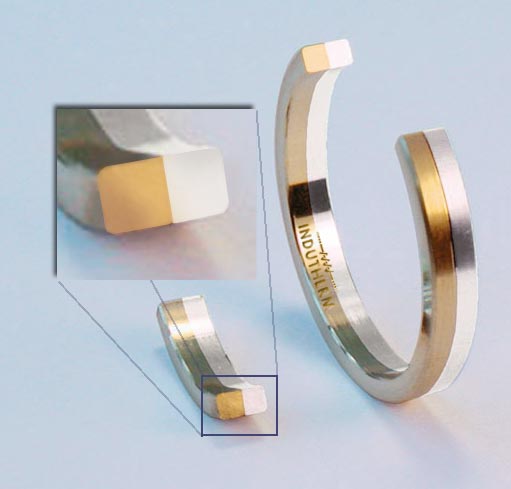
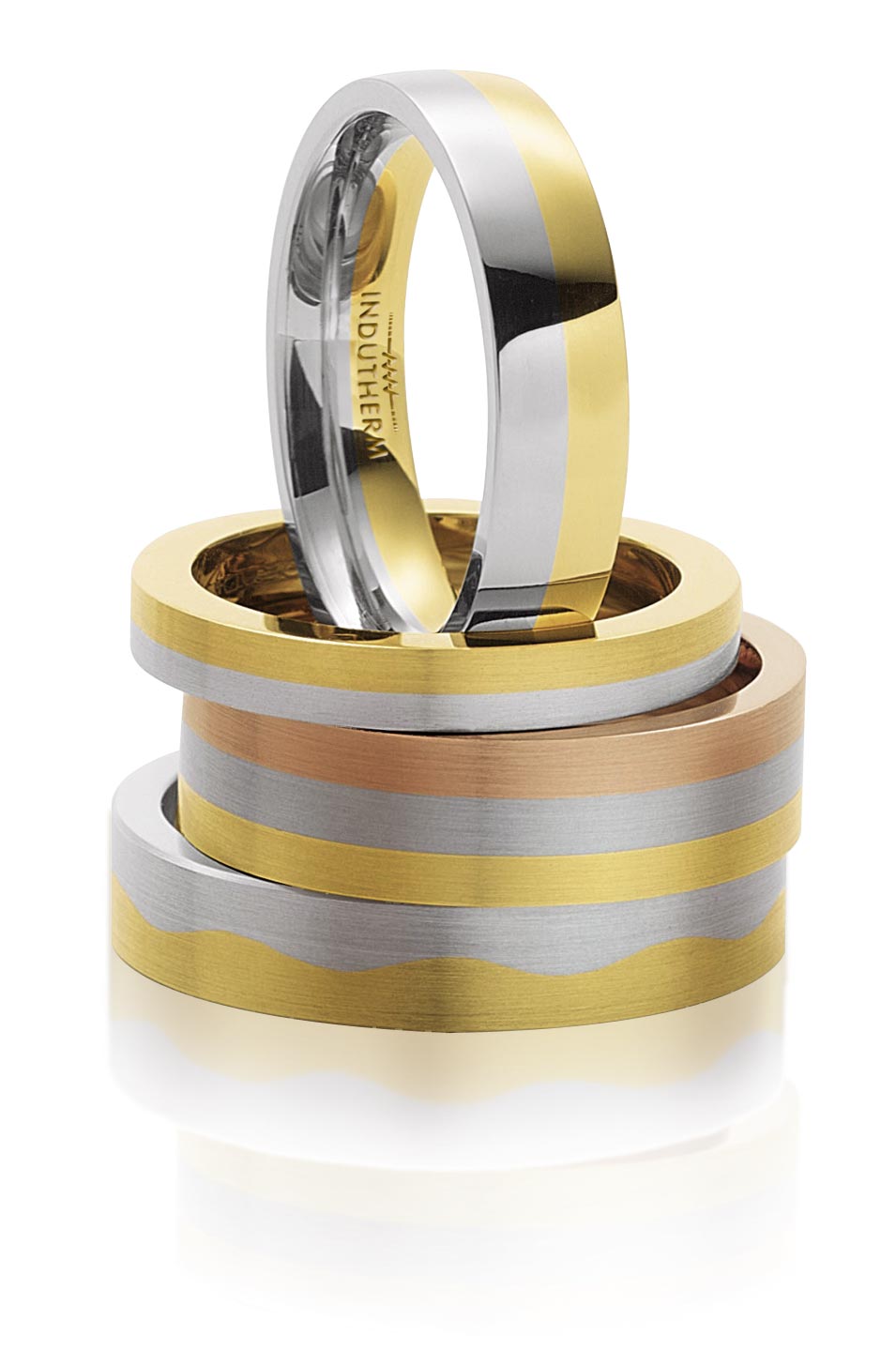
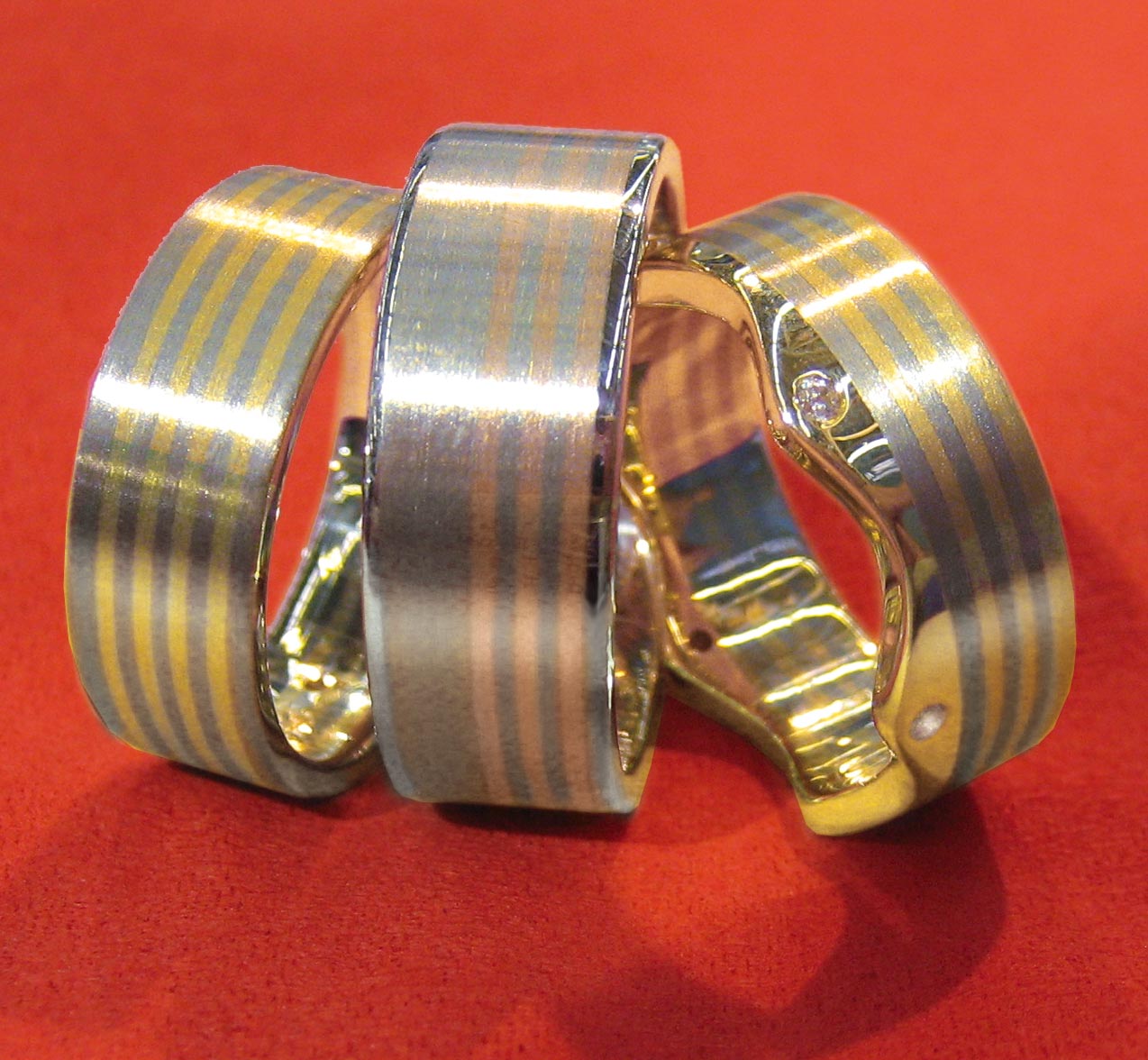
Data Overview of SU-Series
■ standard equipment, ○ optional, - not availableSU 450 | SU 450 XL | |
Power
|
||
Temperature max. | 1300° C | 1300° C |
Power max. / electrical connection | 4,5 kW (3x400 V) | 4,5 kW (3x400 V) |
Capacity
|
||
Sintering processes per hour | ≈ 10 | ≈ 10 |
Diffusion bonding up to Ø mm | 35 | 70 |
Operation and Control
|
||
Reduction control | ■ | ■ |
Control system | by LCD-display, full text readout | by LCD-display, full text readout |
Electronic fix stop | ■ | ■ |
Automatic process stop | ■ | ■ |
Programs | 100 | 100 |
Quality Assurance
|
||
RS 232, Ethernet, USB interface, diagnostic system | ■ | ■ |
Data printer | ■ | ■ |
GSM-modem for remote service | ○ | ○ |
DMS
|
○ | ○ |
InduthermCloud | ○ | ○ |
iThermControl | ○ | ○ |
Accesories
|
||
Vacuum pump | ○ | ○ |
Water chiller | ○ | ○ |
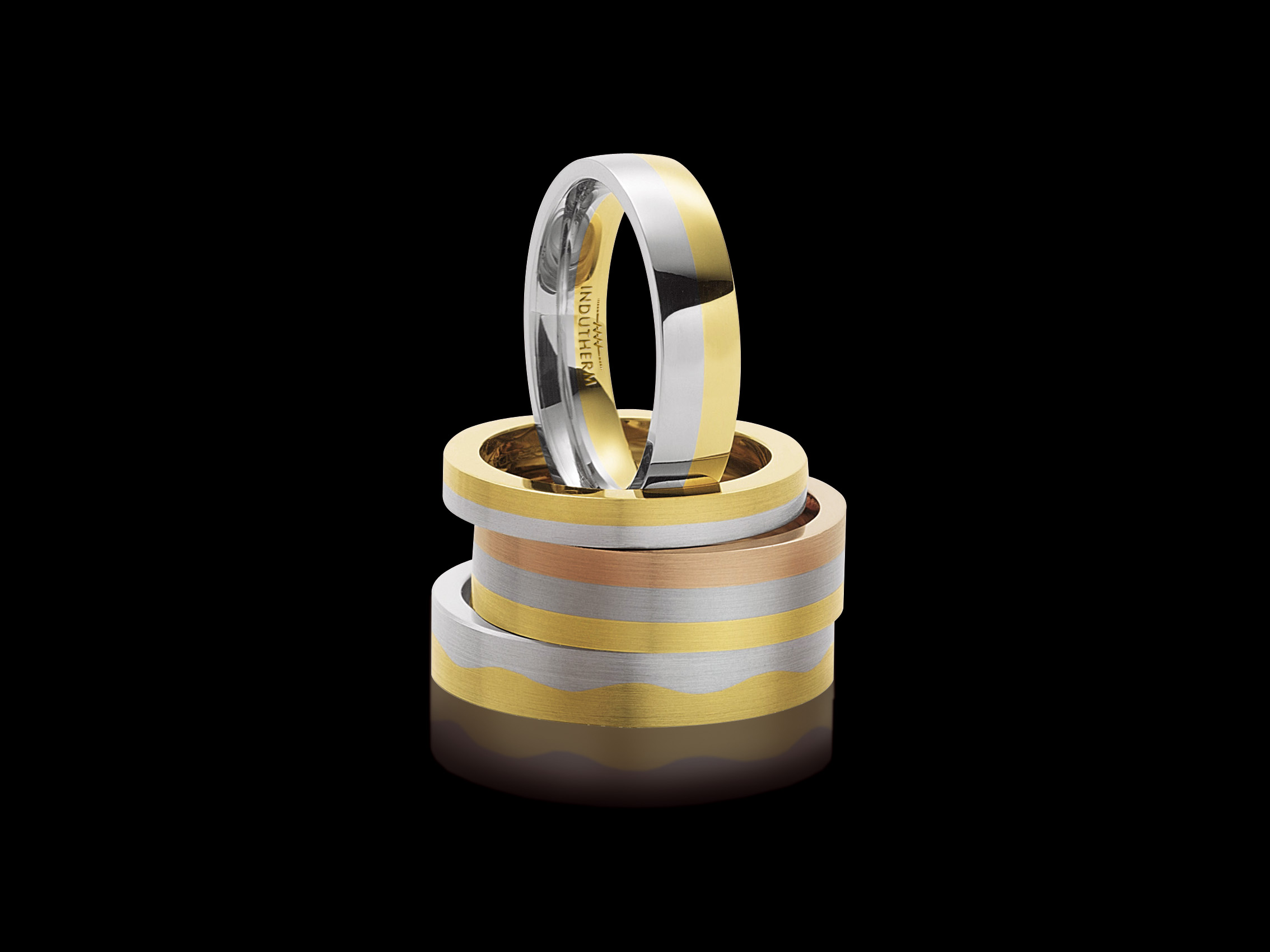
Find more about SU-Series
We offer various options for diffusion welding:
The special sintering systems (SU series) and the sintering kit for converting existing casting systems.
The Sinter-Kit
The sinter kit can be installed in existing Indutherm casting systems of types VC 200 - VC 680 V and in continuous casting systems. The conversion to sintering operation or the retrofitting only takes a few minutes.
The sinter kit can be used to produce occasional diffusion welds and smaller series. However, for larger production volumes, our SU 450 and SU 450 XL sintering systems are recommended.
Sintering plants SU 450/SU 450 XL
Highly sensitive sensors constantly monitor both the SU 450 for rings and the 450 XL (for rings and bracelets).
Compresses the inserted rings and shows the values in real time on the display. This means that the temperature can be regulated to the exact degree until the reduction begins.
When the predefined reduction value is reached, between 0.1 mm and 0.3 mm depending on the structure and alloy combination, the process is automatically ended, thus preventing excessive deformation. The sintering process takes place under a vacuum or protective gas atmosphere to avoid oxidation of the metals.
The “sensor control system” saves time and materials: on the one hand by quickly and loss-free definition of the process parameters, and on the other hand by the consistently high quality in ongoing sinter production. The post-processing effort is therefore significantly reduced, as is the loss of material during subsequent diamond cutting or turning.
-
SU 450
On the SU 450, the sensors constantly monitor the compression of the rings used shows the values in real time on the display. This means the temperature can be adjusted to the exact degree beginning Reduction can be regulated.
When the predefined reduction value is reached, depending on the structure and Alloy combination between 0.1 mm and 0.3 mm, the process will automatically stop, one too This excludes severe deformation.
More about SU 450
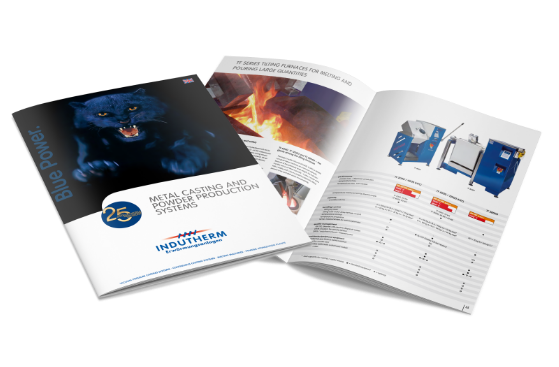