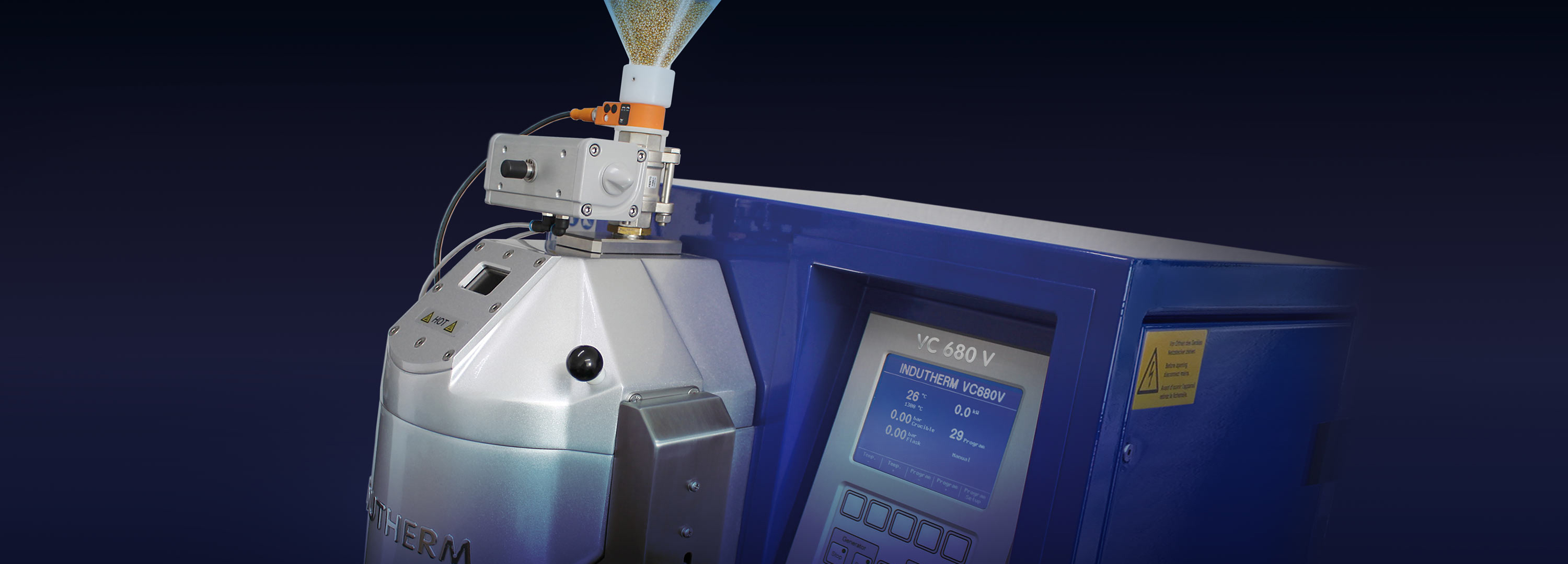
Highly efficient operating concept
The right machine for every application
The range of our VC series systems extends from small to very large capacities, from semi-automatic systems to solutions for fully automatic casting production. Sophisticated functional details create the basis for optimizing each casting for its individual properties.
Separate locking systems for “overlapping” casting
All Indutherm VC systems have separate locking systems for the melting and cuvette chambers, enabling significant time savings through “overlapping” pouring: While the cuvette remains in the vacuum chamber for a few minutes after pouring, the next batch can be filled and heated up.
Pneumatic bell lock and automatic locking system
The melting chambers of all VC systems are closed with a pneumatic system. VC 650 V and VC 680 V are also equipped with an automatic locking system.
Automatic cuvette and chamber lift
To swivel in the vacuum chamber, the cuvette inserted is lowered and then docked automatically. When the chamber is opened, the cuvette is raised for easy removal. This means the economical cuvettes can be used without a flange.
Program control for fast and certified productions
Thanks to the control panel with full-text LCD display, all programs and parameters can be set very easily and practically. The semi-automatic systems have temperature programs. The fully automatic systems have a program control system that includes all parameters.
Up to 100 casting programs ensure quick operation and uniform casting results. The parameters are pre-programmed for the most important alloys, e.g. B. for AGS, Alpha Plus, Heraeus, Legor and
Pandor alloys. In practice, this means: Good casting results can be expected from the first cuvette without expensive preliminary tests. The program control and the built-in data printer ensure a high level of security and precise process logging.
Ready for future standards
Like all of our systems, the VC series is equipped with software and interface management that allows remote maintenance and service and forms the basis for future networking with other systems.
Controlling the pressure conditions – important for the perfect casting result
Automatic vacuum and overpressure in the melting and cuvette chambers
The vacuum in the melting chamber ensures that the metal is degassed and prevents unwanted oxidation during melting (an oxygen-poor atmosphere is particularly important when melting copper-containing alloys). The vacuum in the cuvette chamber improves mold filling, especially when casting delicate parts, and prevents annoying air pockets. In addition, the system switches to overpressure in the melting chamber, thus increasing the pressure difference.
Oxidation reduction after casting
This special system eliminates the risk of oxidation while the cuvette cools.
Turbulence reduction software
TRS ensures a faster and more consistent flow of metal. It improves mold filling and prevents parts of the plaster mold from breaking off at critical points and becoming trapped in the casting.
Turbo Pressure / Turbo Pressure PLUS
The turbo pressure function optimizes the casting of very small and delicate objects and guarantees perfect casting with stones in jewelry production. With Turbo-Pressure, a precisely defined and extremely rapid pressure build-up is achieved during pouring. With all program-controlled VC models, Turbo-Pressure is automatically started at the same time, exactly to the second, depending on the program. The Turbo Pressure PLUS system also allows higher and faster pressure build-up.
HSC – High Speed Casting
HSC improves mold filling and surface quality of small parts or those with large and smooth surfaces. HSC makes it possible to cast processed colored stones at low temperatures.
Precise temperature control
Dual temperature control
The temperature measurement in both the crucible wall and in the crucible center (integrated in the closure rod) ensures strict adherence to the preselected temperature range.
Cuvette temperature measurement
Up until now, cuvettes with incorrect or different temperatures were a safety risk. When casting very small or delicate parts, the correct cuvette temperature is crucial. Measuring the cuvette temperature (standard for VC 650 V and VC 680 V) now provides the decisive plus in safety: the temperature of the cuvette can be checked with an accuracy of one degree.
Vibration technology for better casting results
The Indutherm vibration system
- Vibration during casting improves material flow and thus mold filling.
- The density of the castings is higher and more uniform.
- The porosity is significantly reduced.
- 50% smaller grain sizes
- reduced risk of breakages (hot cracks)
- Cast parts have better tension and elastic properties, which makes them easier to process
In practice this means: higher and more consistent quality, less scrap, less post-processing, better formability. A customer in the USA found that the Indutherm vibration technology reduced overall production time, including post-processing, by 25%.
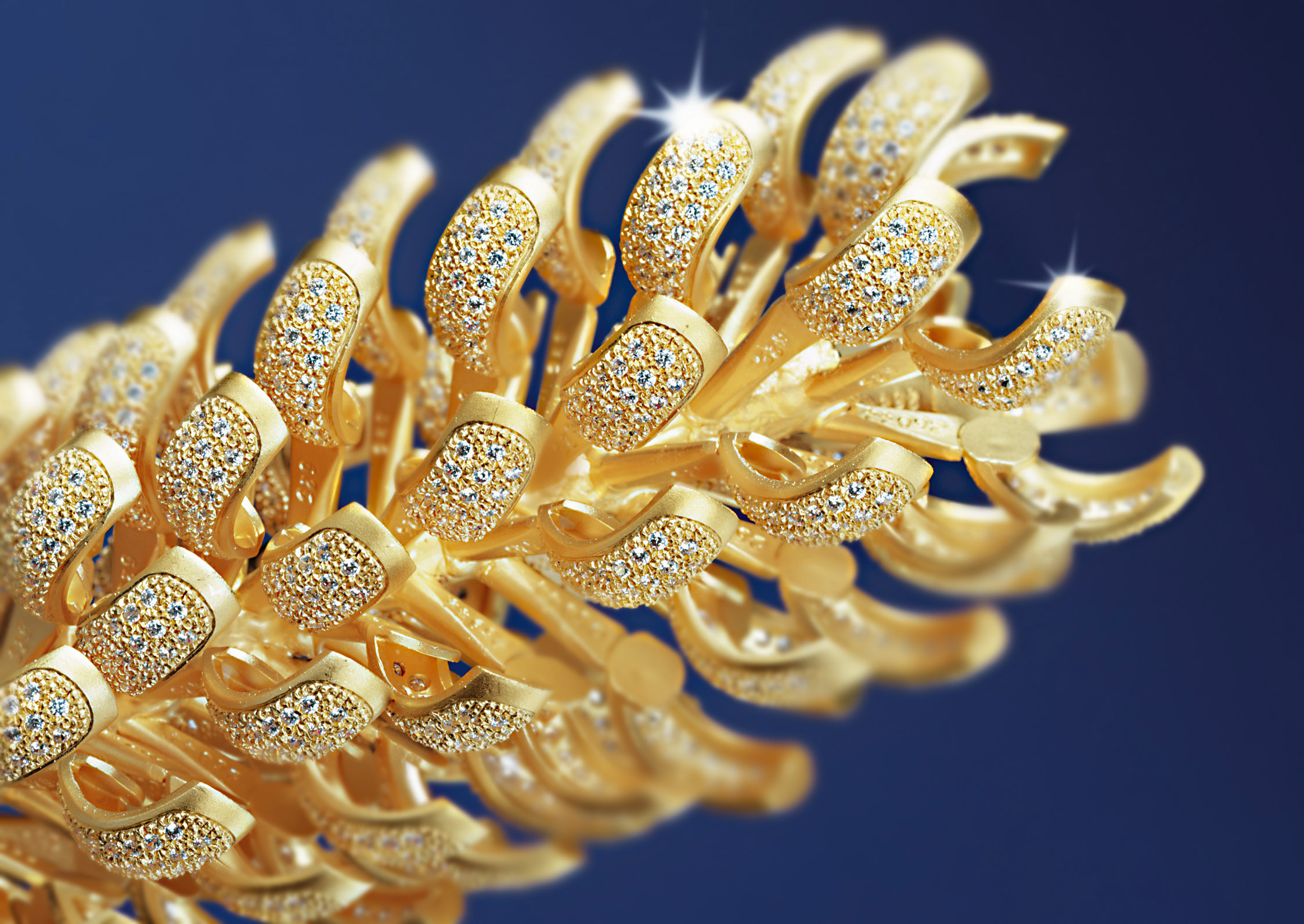
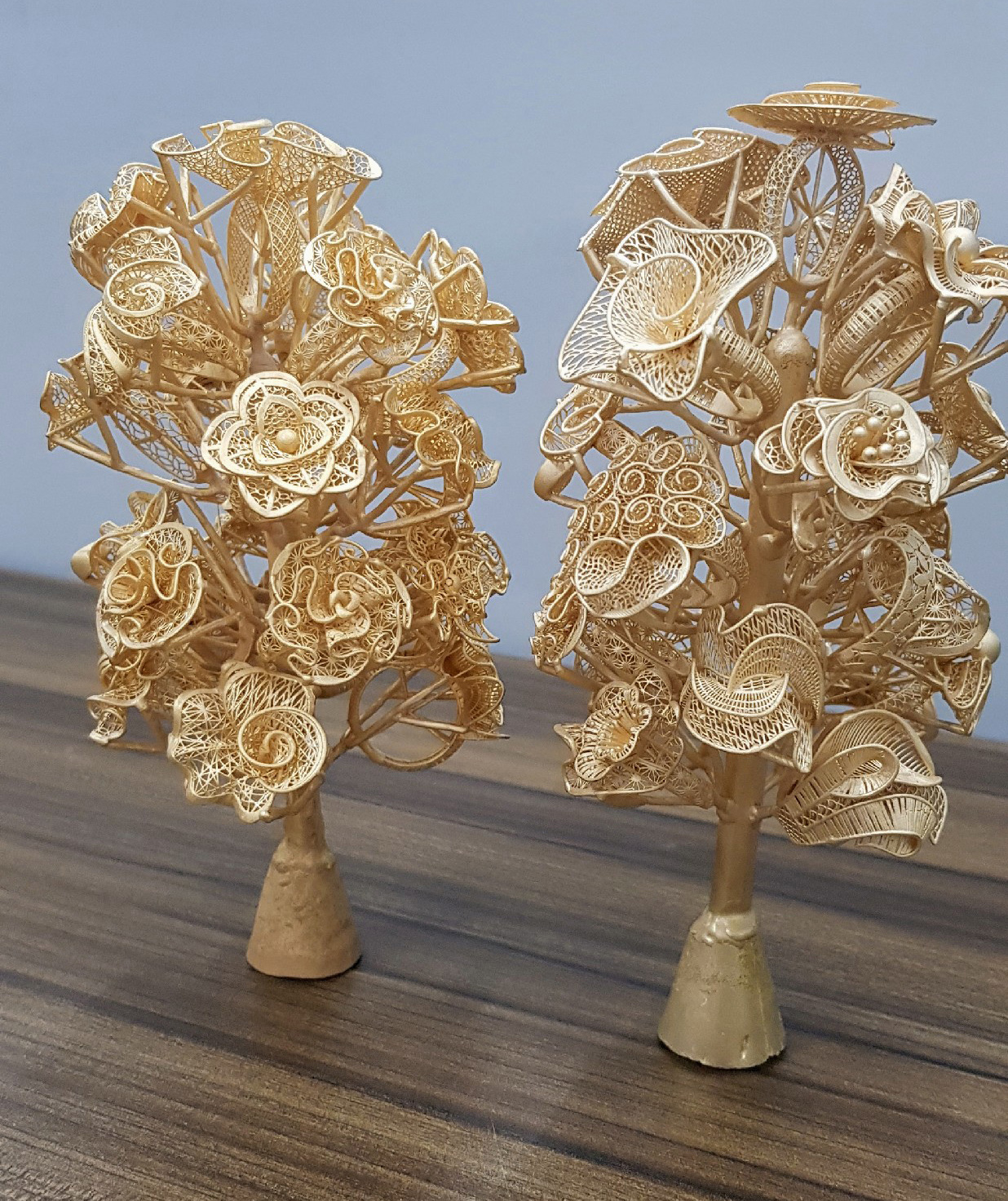
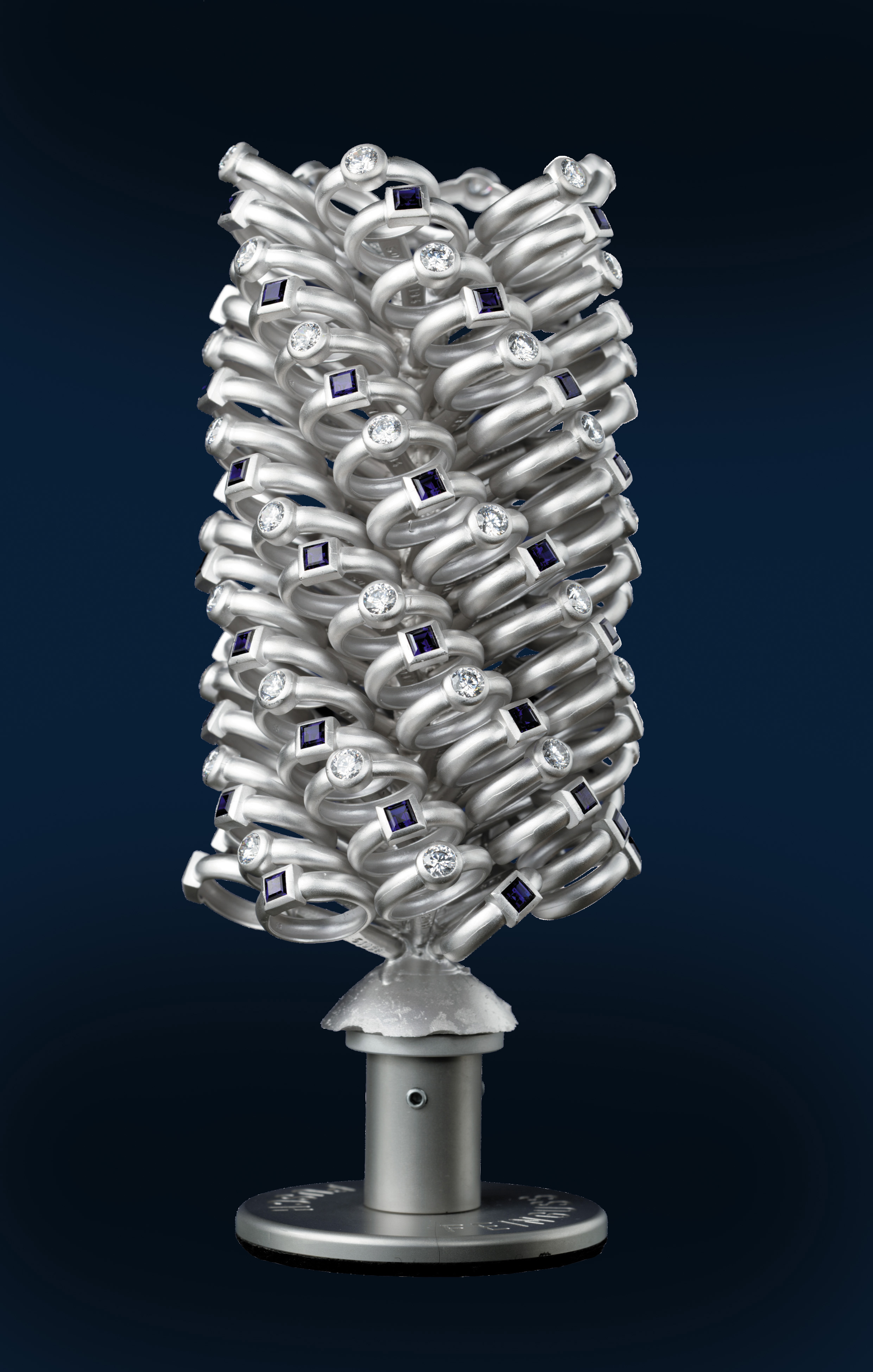
Data Overview of VC400
■ standard equipment, ○ optional, - not available
VC400 | VC450 | VC500 | VC450V | VC460V | VC480V | VC650V | VC680V | VC1000V | VC25000 | VC3000V | VC650VHTC | VC680VHTC | VC1000VHTC | VC12000HTC | VC3000VHTC | |
Power
|
||||||||||||||||
Power max. / electrical connection | 3.5 kW (230 V)|4.5 kW (3x400 V) | 4,5 kW (3x400 V) | 10 kW (3x400 V)|10 kW(3x208 V) | 4,5 kW (3x400 V) | 4,5 kW (3x400 V) | 8 kW (3x400 V) | 12 kW (3x400v) | 12 kW (3x400v) | 20 kW (3x400 V) | 60 kW (3x400 V) | 30 kW (3x400 V) | 12 kW (3x400v) | 12 kW (3x400v) | 20 kW (3x400 V) | 40-60 kW (3x400 V) | 30 kW (3x400 V) |
Temperature max. | 1400° C | 1600° C | ||||||||||||||
Temperature max. indirect inductive heating HTC | 1850° C | 1850° C | 1850° C | 1850° C | 2000° C | 2000° C | 2000° C | 1850° C | 2000° C | |||||||
Capacity
|
||||||||||||||||
Crucible Volume | ■ 170 ccm = 2,5 kg Au 18 ct / 1,5 kg Cu* | 170 ccm = 2,5 kg Au 18 ct / 1,5 kg Cu* | ■ 245 ccm = 3,6 kg Au 18 ct / 2 kg Cu* ○ 386 ccm = 5,8 kg Au 18 ct / 3,3 kg Cu* |
170 ccm = 2,5 kg Au 18 ct / 1,5 kg Cu* | 170 ccm = 2,5 kg Au 18 ct / 1,5 kg Cu* | ■ 170 ccm = 2,5 kg Au 18 ct / 1,5 kg Cu* ○ 245 ccm = 3,6 kg Au 18 ct / 2 kg Cu* |
■ 245 ccm = 3,6 kg Au 18 ct / 2 kg Cu* ○ 386 ccm = 5,8 kg Au 18 ct / 3,3 kg Cu* ○ 700 ccm =10,5 kg Au 18 ct / 6 kg Cu* |
■ 245 ccm = 3,6 kg Au 18 ct / 2 kg Cu* ○ 386 ccm = 5,8 kg Au 18 ct / 3,3 kg Cu* ○ 700 ccm =10,5 kg Au 18 ct / 6 kg Cu* |
1,5 l (1,7) = 4 kg Al / 12 kg Cu / 12 kg steel* | 25 l = 65 kg Al / 200 kg Cu* | 3,4 l (3,9) = 8,5 kg Al / 25 kg Cu / 25 kg steel* | ■ 245 ccm = 3,6 kg Au 18 ct / 2 kg Cu* ○ 386 ccm = 5,8 kg Au 18 ct / 3,3 kg Cu* ○ 700 ccm =10,5 kg Au 18 ct / 6 kg Cu* |
■ 245 ccm = 3,6 kg Au 18 ct / 2 kg Cu* ○ 386 ccm = 5,8 kg Au 18 ct / 3,3 kg Cu* ○ 700 ccm =10,5 kg Au 18 ct / 6 kg Cu* |
1,5 l (1,7) = 4 kg Al / 12 kg Cu / 12 kg steel* | 12 l (14 ) = 30 kg Al / 90 kg Cu / 90 kg steel* | 3,4 l (3,9) = 8,5 kg Al / 25 kg Cu / 25 kg steel* |
For use of molds up to | ø 130 mm / 240 mm h | ø 130 mm / 240 mm h | ■ ø 130 mm / 240 mm h ○ ø 160 mm / 400 mm h |
■ ø 130 mm / 240 mm h ○ ø 160 mm / 400 mm h |
■ ø 130 mm / 240 mm h ○ ø 160 mm / 400 mm h |
■ ø 130 mm / 240 mm h ○ ø 160 mm / 400 mm h |
ø 250 mm / 500 mm h | ø 600 mm / 800 mm h | ø 450 mm / 600 mm h | ■ ø 130 mm / 240 mm h ○ ø 160 mm / 400 mm h |
■ ø 130 mm / 240 mm h ○ ø 160 mm / 400 mm h |
ø 250 mm / 500 mm h | ø 600 mm / 800 mm h | ø 450 mm / 600 mm h | ||
For use of molds | up to ø 130 mm / 240 mm h | ■ up to ø 130 mm / 240 mm h ○ bis ø 160 mm / 400 mm h | ||||||||||||||
Operation and Control
|
||||||||||||||||
Maximum pressure | ■ up to 1,5 bar ○ up to 3,0 bar | ■ up to 1,5 bar ○ up to 3,0 bar | ■ up to 1,5 bar ○ up to 3,0 bar | ■ up to 1,5 bar ○ up to 3,0 bar | ■ up to 1,5 bar ○ up to 3,0 bar | ■ up to 1,5 bar ○ up to 3,0 bar | 3 bar | 3 bar | 0,5 bar | 0,3 bar | 0,3 bar | 3 bar | 3 bar | 0,5 bar | 0,3 bar | 0,3 bar |
Automatic mold and chamber lift | ■ | - | ■ | - | - | ■ | ■ | ■ | ■ | ■ | ||||||
Control system | by LCD-display, full text readout | by LCD-display, full text readout | by LCD-display, full text readout | by LCD-display, full text readout | by LCD-display, full text readout | by LCD-display, full text readout | by LCD-display, full text readout | by LCD-display, full text readout | by LCD-display, full text readout | by LCD-display, full text readout | by LCD-display, full text readout | by LCD-display, full text readout | by LCD-display, full text readout | by LCD-display, full text readout | by LCD-display, full text readout | by LCD-display, full text readout |
Automatic bell lock | ■ | ■ | ■ | ■ | ■ | ■ | ■ | ■ | ■ | ■ | ■ | ■ | ■ | ■ | ■ | ■ |
Dual temperature control | ○ | ○ | ○ | ○ | ○ | ○ | ○ | ○ | ■ | ■ | ■ | ○ | ○ | ■ | ■ | ■ |
Turbo Pressure Function | ■ | ■ | ■ | ■ | ■ | ■ | ■ | ■ | ■ | ■ | ■ | ■ | ■ | ■ | ■ | ■ |
Mold temperature measurement | - | - | - | - | ■ | ■ | ■ | ■ | ||||||||
HSC (High Speed Casting) feature | ○ | ○ | ○ | ○ | ○ | ○ | ○ | ○ | ||||||||
Turbo Pressure PLUS system | - | - | - | ○ | ■ | ■ | ■ | ■ | ||||||||
Vibration technology | - | ■ | - | ■ | standard equipment Sweep Mode | standard equipment Sweep Mode | ■ | ■ | ■ | standard equipment Sweep Mode | standard equipment Sweep Mode | ■ | ■ | ■ | ||
Automatic mold and chamber lift | ■ | ■ | ■ | ■ | ■ | ■ | ■ | - | ■ | ■ | ■ | ■ | - | ■ | ||
Automatic feeding system w/ autom. sealing rod | - | - | - | - | - | ■ | - | ■ | ||||||||
Automatic closing system | - | - | - | - | ■ | ■ | ■ | ■ | ||||||||
Programs | 20 | 20 | 20 | 20 | 20 | 100 | 100 | 100 | 100 | 100 | 100 | 100 | 100 | 100 | 100 | 100 |
Mold temperature measurement | ■ | ■ | ||||||||||||||
Temp. measurement by optical pyrometer | 1400° C | 1400° C | 1400° C | 1600° C | 1700° C | 1700° C | 1500° C | 1300° C | 1500° C | 1700° C | 1700° C | 1500° C | 1300° C | 1500° C | ||
Turbulence reduction software | ■ | ■ | ■ | ■ | ■ | ■ | ■ | ■ | ■ | ■ | ■ | ■ | ■ | ■ | ■ | ■ |
Quality Assurance
|
||||||||||||||||
RS 232, Ethernet, USB interface, diagnostic system | ■ | ■ | ■ | ■ | ■ | ■ | ■ | ■ | ■ | ■ | ■ | ■ | ■ | ■ | ■ | ■ |
Data printer | - | ○ | - | ○ | ○ | ○ | ■ | ■ | ■ | ■ | ■ | ■ | ■ | ■ | ■ | ■ |
GSM-modem for remote service | ○ | ○ | ○ | ○ | ○ | ○ | ■ | ■ | ■ | ■ | ■ | ■ | ■ | ■ | ■ | ■ |
DMS
|
■ | ■ | ■ | ■ | ■ | ■ | ■ | ■ | ■ | ■ | ■ | ■ | ■ | ■ | ■ | ■ |
InduthermCloud | ○ | ○ | ○ | ○ | ○ | ○ | ○ | ■ | ○ | ○ | ○ | ○ | ■ | ○ | ○ | ○ |
iThermControl | ○ | ○ | ○ | ○ | ○ | ○ | ○ | ■ | ○ | ■ | ||||||
Accesories
|
||||||||||||||||
Sintering / diffusion bonding kit | ○ | ○ | ○ | ○ | ○ | ○ | ○ | ○ | ○ | ○ | ||||||
Granulation tank | ○ | ○ | ○ | ○ | ○ | ○ | ○ | ○ | ○ | ○ | ○ | ○ | ○ | ○ | ○ | ○ |
Granulation tank with flake option | ○ | ○ | ○ | ○ | ○ | ○ | ○ | ○ | ○ | ○ | ○ | ○ | ○ | ○ | ○ | ○ |
Vacuum pump | ○ | ○ | ○ | ○ | ○ | ○ | ○ | ○ | ○ | ○ | ○ | ○ | ○ | ○ | ○ | ○ |
Water chiller | ○ | ○ | ○ | ○ | ○ | ○ | ○ | ○ | ○ | ○ | ○ | ○ | ○ | ○ | ○ | ○ |
Also available as granulating unit | - | GU 500 |
* flüssiges Metall bis Tiegeloberkante
** mit zusätzlichem Gastank für Turbo Pressure PLUS
Die auf dieser Seite veröffentlichten Maschinenbeschreibungen und technischen Daten erheben keinen Anspruch auf Vollständigkeit. Sie können sich im Zuge der Weiterentwicklung ändern und sind deshalb keine Vertragsgrundlage.Other Advantages of VC400
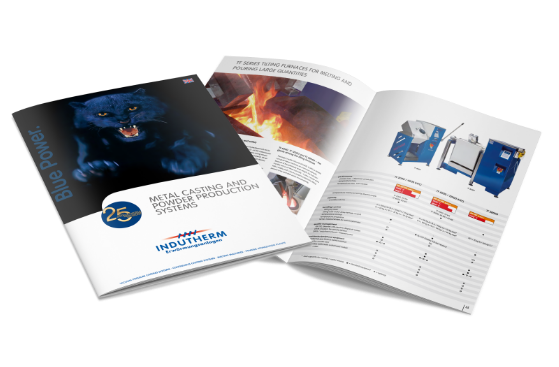