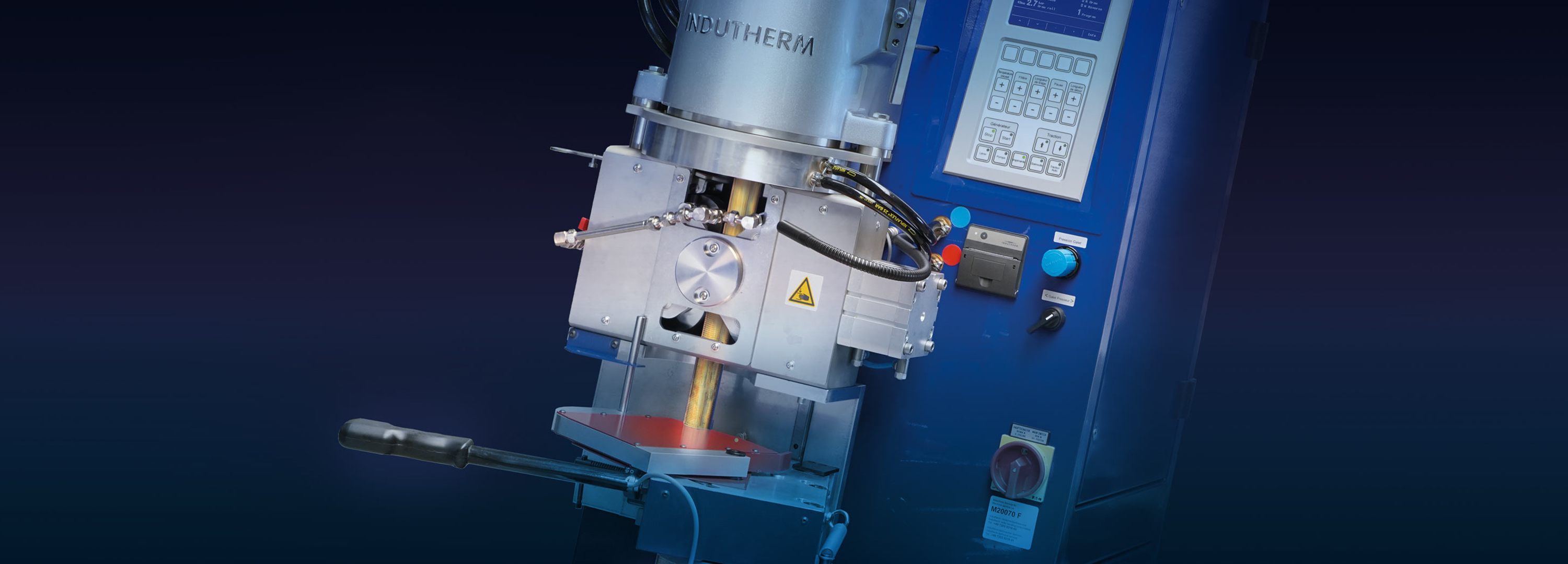
More flexibility, lower costs
With an Indutherm continuous casting machine, you can produce your own alloys or semi-finished products in different shapes and sizes in the shortest time:
- Wires or bars up to ø 90 mm
- Sheet and strips, e.g. ring production, for stamping and pressing
- Tubes, perfect as basic material for cutting in sections for wedding ring production
- Granules and flakes
The use of a continuous casting machine can reduce your investment for material in storage considerably. Your processes will get faster, more flexible and more efficient. Our continuous casting machines are equipped with a number of unique details which substantially improve the quality of the semi-finished material, e.g. the unique vacuum system or the QUATTRO DRIVE drawing system. For details see next page. With a wide range of optionally available equipment the versatility of these machines may be enhanced even more.
Granulation tank and flake kit
The easy to install granulation tank and the flake kit make each CC machine even more versatile.
Sintering kit
Sintering/diffusion bonding is the optimum process for producing multi-coloured rings, mostly sold as wedding rings, or bracelets. Metals are processed under pressure and at temperatures below the solidification point. The pressure is generated pneumatically and not mechanically via a threaded spindle. This means that there is no risk of graphite parts breaking as a result of heat expansion. The fusion between layers has the same durability as the metal itself. The sintering kit is ideal for the occasional diffusion bonding job and for smaller series production.
Bar casting kit
The bar casting kit is developed for casting defined quantities of your alloy into ingot molds or into any other molds. The program control recognizes the applicated equipment and provides the suited parameter settings on the display
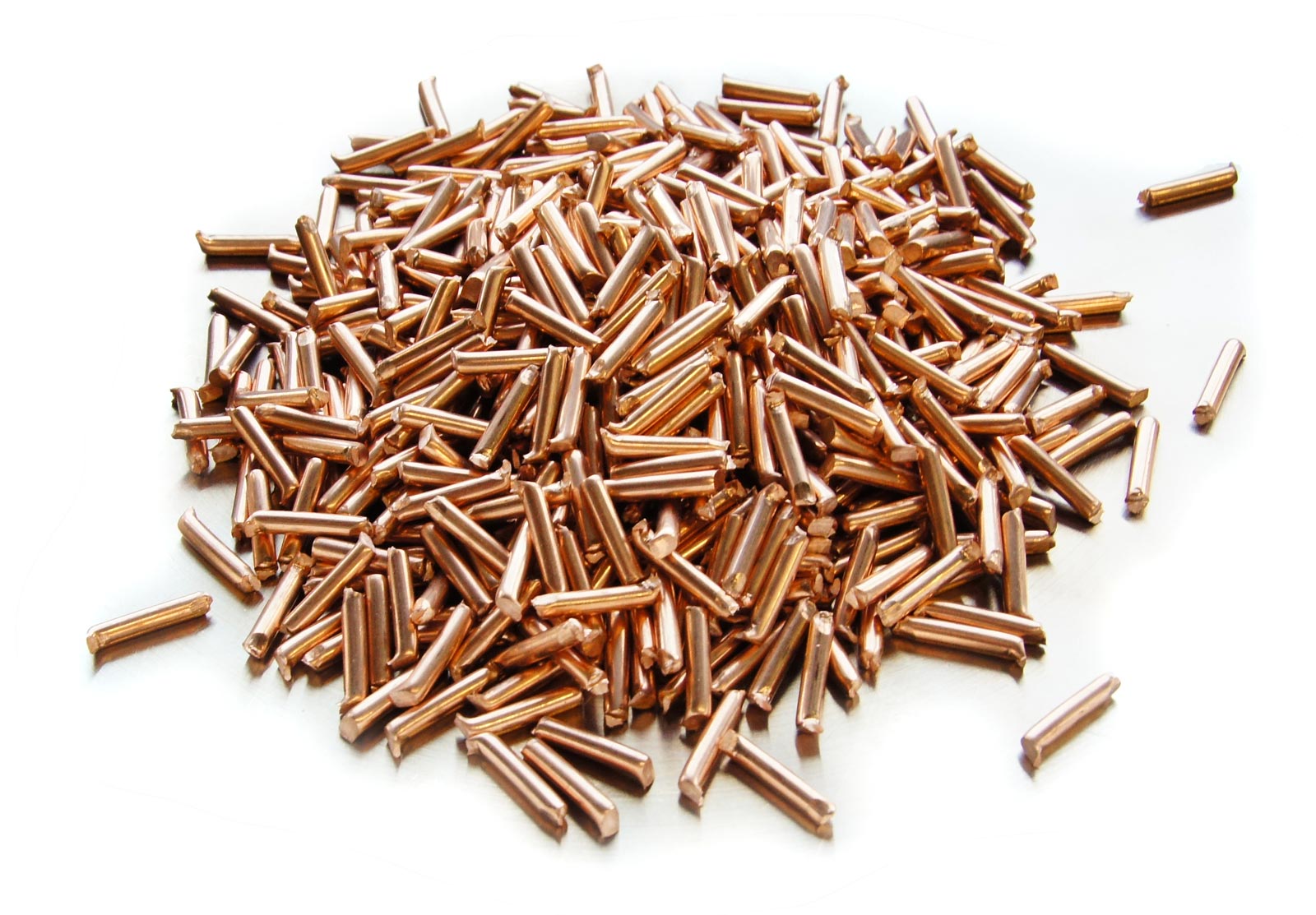
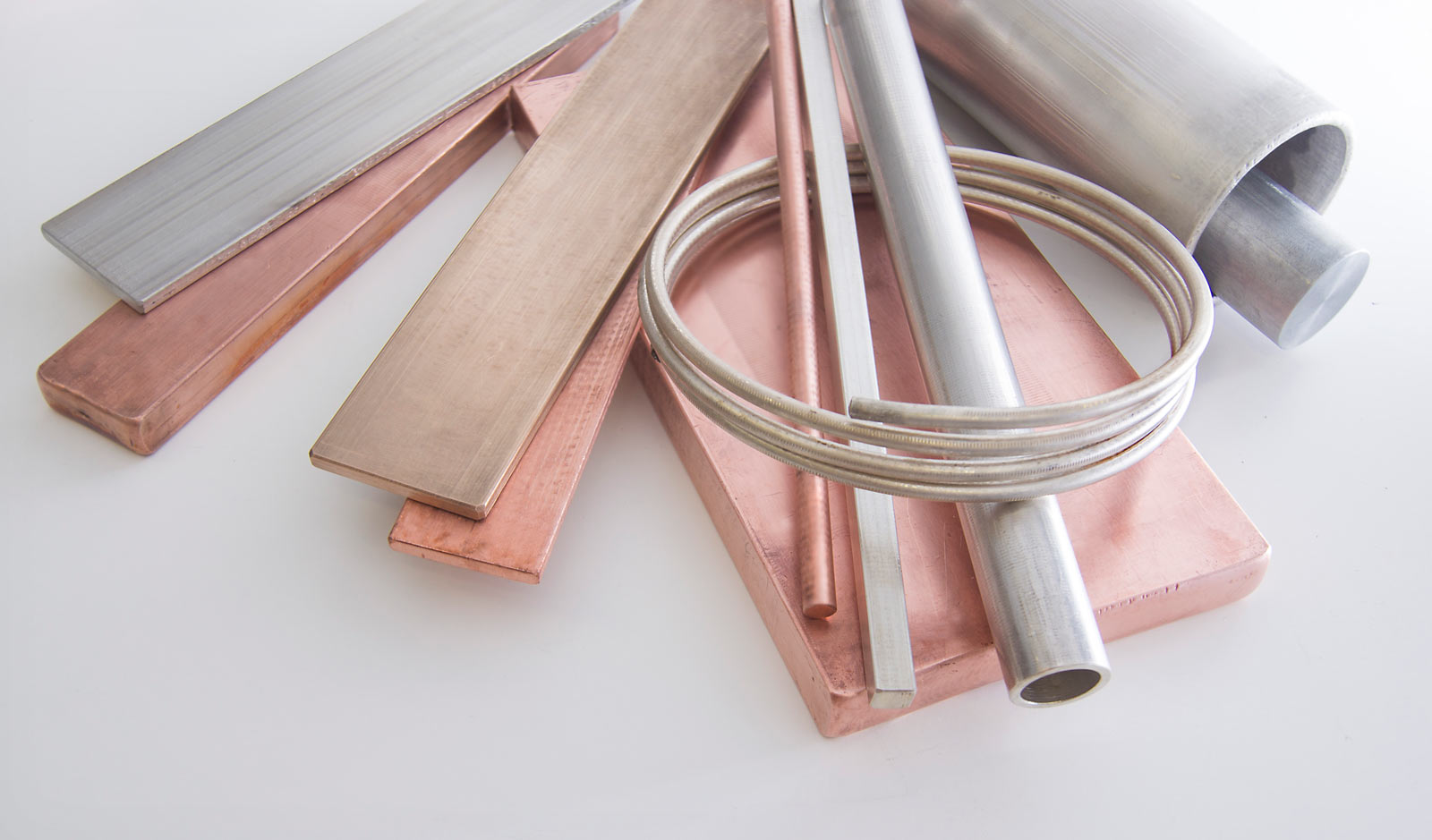
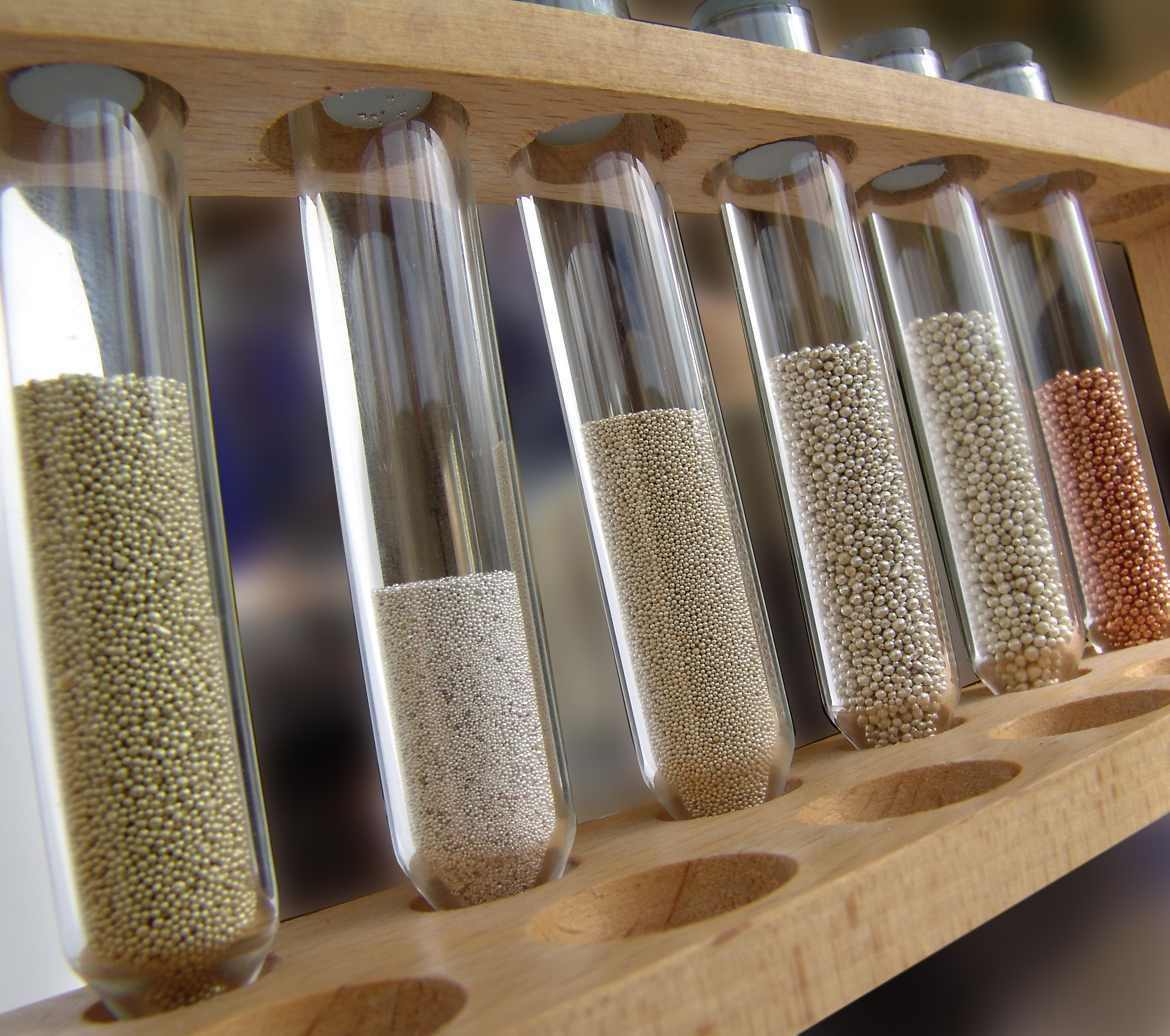
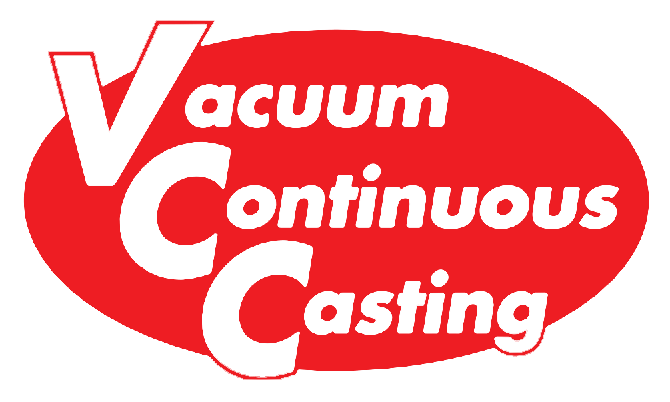
Unique vacuum system
For highest quality of semi-finished material:
To reduce the risk of oxidation during melting and during drawing, we focus on avoiding oxygen contact and on fast reduction of the temperature of the drawn material.
Features for fast temperature reduction:
- Cooling water temperature measurement and automatic flow control
- Optical temperature measurement in the center of the die
- Die cooler
- Additional secondary cooling system at the outlet
Features to avoid oxygen contact:
- Vacuum system for the melting chamber – uniquely available for Indutherm continuous casting machines (VCC versions)
- _ Feeding system for re-charging without oxygen contact and with constant vacuum in the melting chamber
- Inert gas system for the melting chamber
- Inert gas flushing at the die
- Optical die temperature measurement
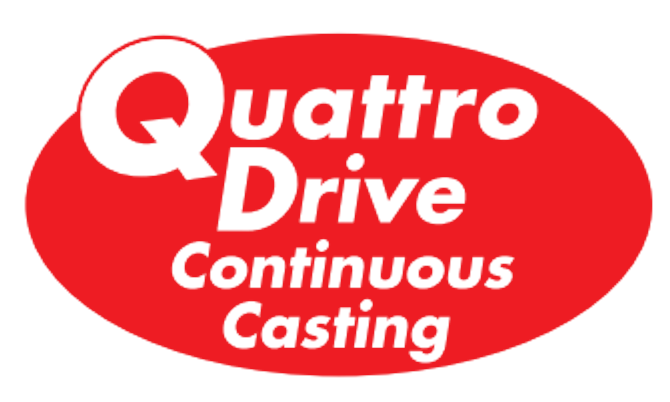
Quattro Drive System
On each of our continuous casting machines, the material is drawn off by motor driven and pneumatically pressed-on feed rolls. A bar end control sensor stops automatically when the molten material is spent.
The optional Quattro Drive drawing unit with four instead of two motor driven feed rolls produces smoother tubes and sheeting with reduced marks of transportation.
Numerous options for targeted produktion of semi-finished parts
Bending unit
Using the bending unit attached to the bottom drawer,
the material can be bent without mechanical force on
the die.
Hydraulic cutter
The hydraulic cutter is suited for cutting wires into
pre-defined sections.
Continuous casting and cutting to size in one operation!
Flying saw for shorting during drawing
The swiveling electric saw (large picture above) moves synchronously with the drawn bar or tube. This way you can cut your material into defined sections during drawing. You don’t need to stop the continuous casting process when maximum length is reached.
Data Overview of (V)CC-Series
■ standard equipment, ○ optional, - not available
CC 400 | CC 1000 | VCC 1000 | CC 3000 | VCC 3000 | CC 12000 | VCC 12000 | |
Power
|
|||||||
Temperature max. | 1500° C | 1500° C | 1500° C | 1500° C | 1500° C | 1500° C | 1500° C |
Power max. / electrical connection | 15 kW (3x400 V)|15 kW (3x208 V) | 20 kW (3x400 V) | 20 kW (3x400 V) | 30 kW (3x400 V) | 30 kW (3x400 V) | 40-60 kW (3x400 V) | 40-60 kW (3x400 V) |
Capacity
|
|||||||
Crucible Volume | ■ 245 ccm = 3,6 kg Au 18 ct / 2 kg Cu* ○ 386 ccm = 5,8 kg Au 18 ct / 3,3 kg Cu* ○ 700 ccm =10,5 kg Au 18 ct / 6 kg Cu* |
1,5 l = 4 kg Al / 12 kg Cu * | 1,5 l = 4 kg Al / 12 kg Cu * | 3,4 l = 8,5 kg Al / 25 kg Cu * | 3,4 l = 8,5 kg Al / 25 kg Cu * | 12 l = 30 kg Al / 90 kg Cu * | 12 l = 30 kg Al / 90 kg Cu * |
Wire production up to | Ø 20 mm** | Ø 40 mm** | Ø 40 mm** | Ø 70 mm** | Ø 70 mm** | Ø 70 mm** | Ø 70 mm** |
Tube production up to | Ø 45 mm** | Ø 65 mm** | Ø 65 mm** | Ø 90 mm** | Ø 90 mm** | Ø 90 mm** | Ø 90 mm** |
Sheet production | ■ 50 x 8 mm ○ 60 x 8 mm |
100 x 10 mm | 100 x 10 mm | 130 x 40 mm | 130 x 40 mm | 130 x 40 mm | 130 x 40 mm |
Operation and Control
|
|||||||
Control system | by LCD-display, full text readout | by LCD-display, full text readout | by LCD-display, full text readout | by LCD-display, full text readout | by LCD-display, full text readout | by LCD-display, full text readout | by LCD-display, full text readout |
Programs | 100 | 100 | 100 | 100 | 100 | 100 | 100 |
Vacuum/Inert gas overpressure | - | - | ■ | - | ■ | - | ■ |
Neutral inert gas atmosphere | ■ | ■ | ■ | ■ | ■ | ■ | ■ |
Optical die temperature measurement | ■ | ■ | ■ | ■ | ■ | ■ | ■ |
Die cooler with protective gas flushing | ■ | ■ | ■ | ■ | ■ | ■ | ■ |
Secondary cooler / water collection system | ■ | ■ | ■ | ■ | ■ | ■ | ■ |
End bar sensor | ■ | ■ | ■ | ■ | ■ | ■ | ■ |
Quality Assurance
|
|||||||
RS 232, Ethernet, USB interface, diagnostic system | ■ | ■ | ■ | ■ | ■ | ■ | ■ |
Data printer | ■ | ■ | ■ | ■ | ■ | ■ | ■ |
GSM-modem for remote service | ■ | ■ | ■ | ■ | ■ | ■ | ■ |
DMS
|
■ | ■ | ■ | ■ | ■ | ■ | ■ |
InduthermCloud | ○ | ○ | ○ | ○ | ○ | ○ | ○ |
iThermControl | ○ | ○ | ○ | ○ | ○ | ○ | ○ |
Accesories
|
|||||||
Quattro drive drawing unit | ○ | ○ | ○ | ○ | ○ | ○ | ○ |
Sintering / diffusion bonding kit | ○ | - | - | - | - | - | - |
Granulation tank | ○ | ○ | ○ | ○ | ○ | ○ | ○ |
Granulation tank with flake option | ○ | ○ | ○ | ○ | ○ | ○ | ○ |
Bending-unit | ○ | ○ | ○ | ○ | ○ | ○ | ○ |
Coiling equipment | - | ○ | ○ | ○ | ○ | ○ | ○ |
Simultaneous casting of several wires | - | ○ 3 wires*** | ○ 3 wires*** | ○ 5 wires*** | ○ 5 wires*** | ○ 5 wires*** | ○ 5 wires*** |
Flying saw | ○ | ○ | ○ | ○ | ○ | ○ | ○ |
Pneumatic cutter | ○ | ○ | ○ | ○ | ○ | ○ | ○ |
Vacuum pump | ○ | ○ | ○ | ○ | ○ | ○ | ○ |
Water chiller | ○ | ○ | ○ | ○ | ○ | ○ | ○ |
Water collection system | ○ | ○ | ○ | ○ | ○ | ○ | ○ |
* Liquid metal up to top level of the crucible – other
volumes on request.
** Special dimensions or profiles on demand
*** not in combination with Quattro Drive
Other Advantages of (V)CC-Series
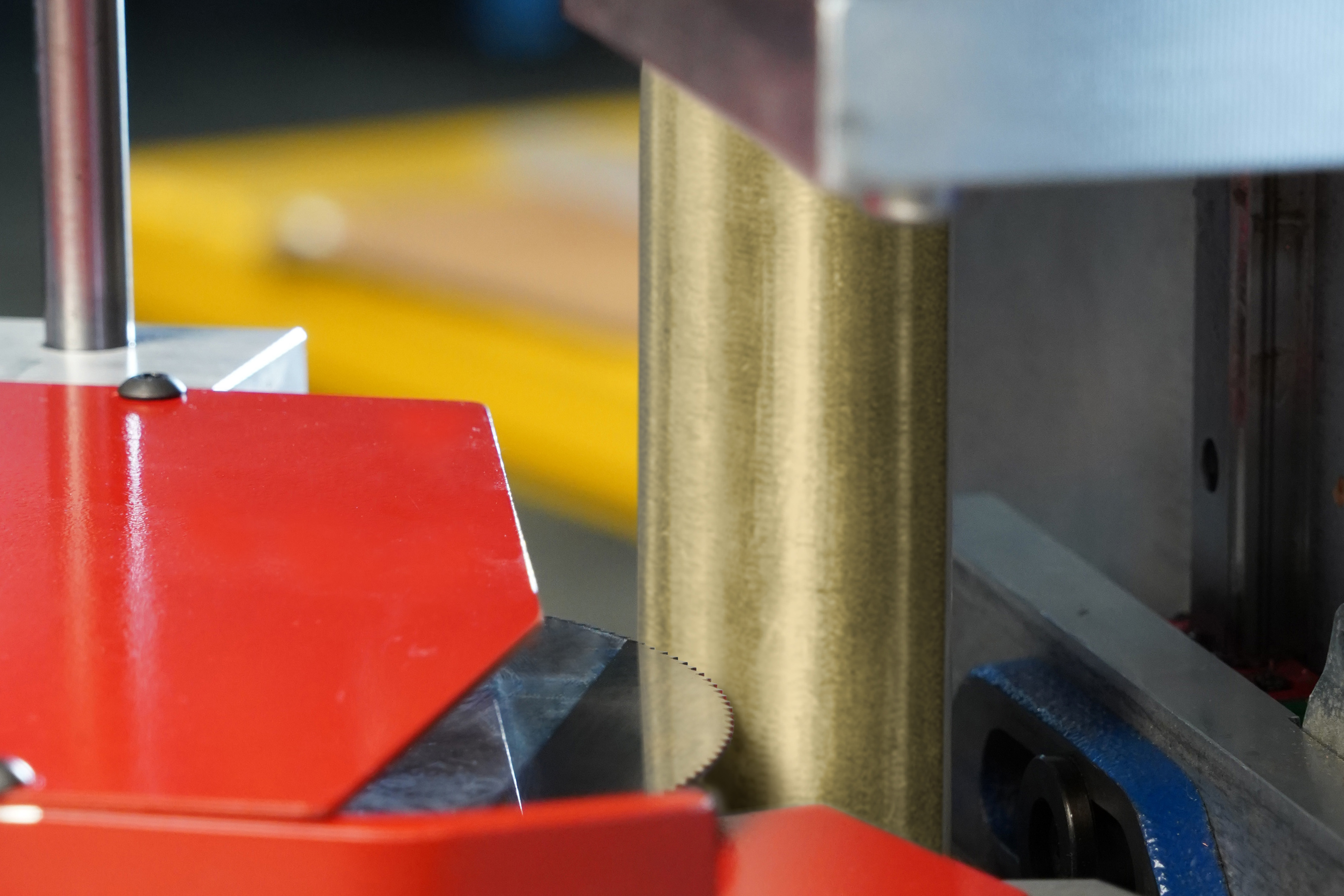
CC/VCC SERIES CONTINUOUS CASTING MACHINES – OUR 5 IN 1 MULTITOOLS
Change Functions within 5 Minutes!
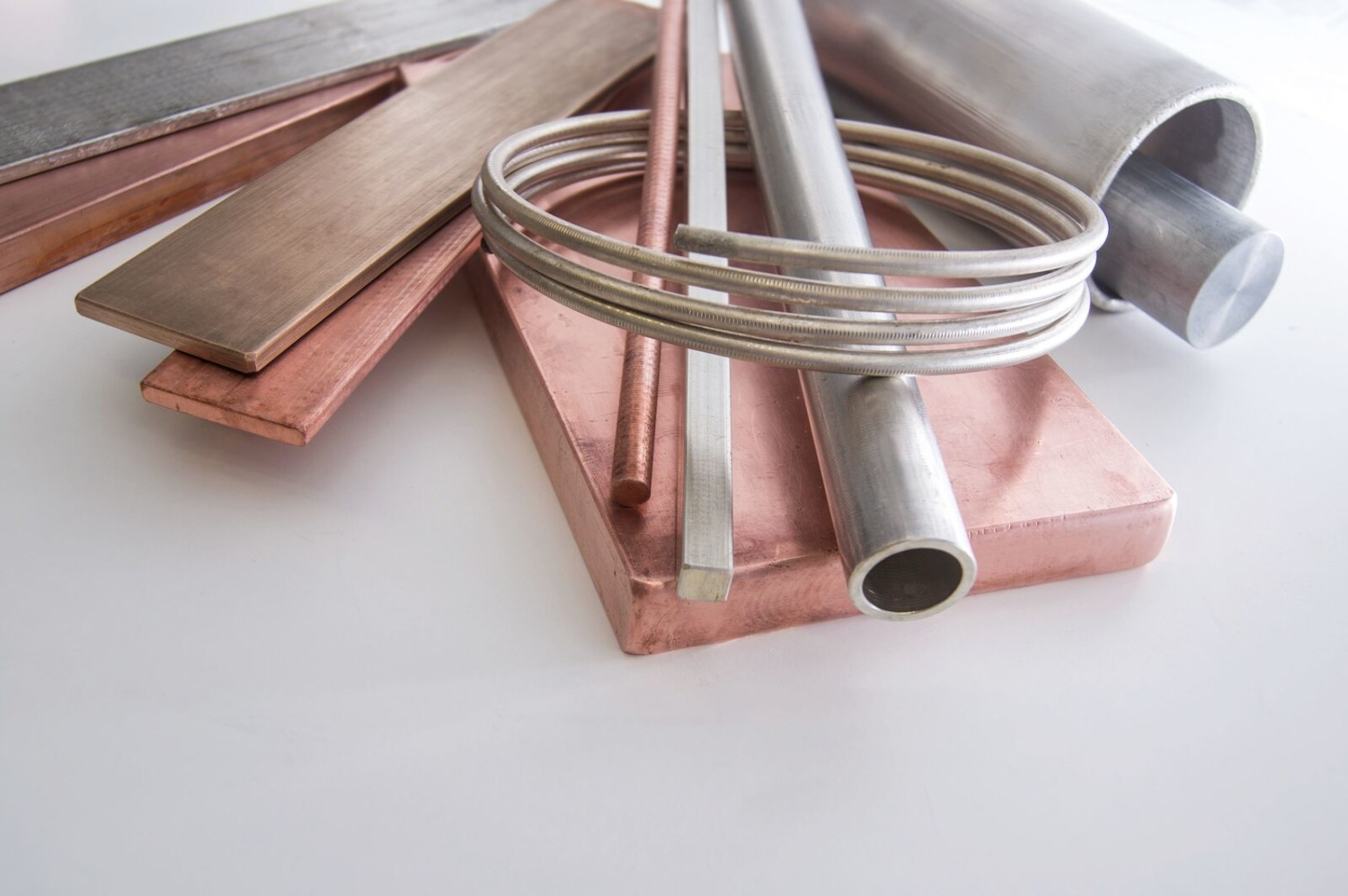
(Vakuum) Continuous Casting of Wire, Sheet and Tubes
with numerous options for cutting or sawing into sections during casting, for bending or coiling. VCC series with inert gas/vacuum system for the melting chamber
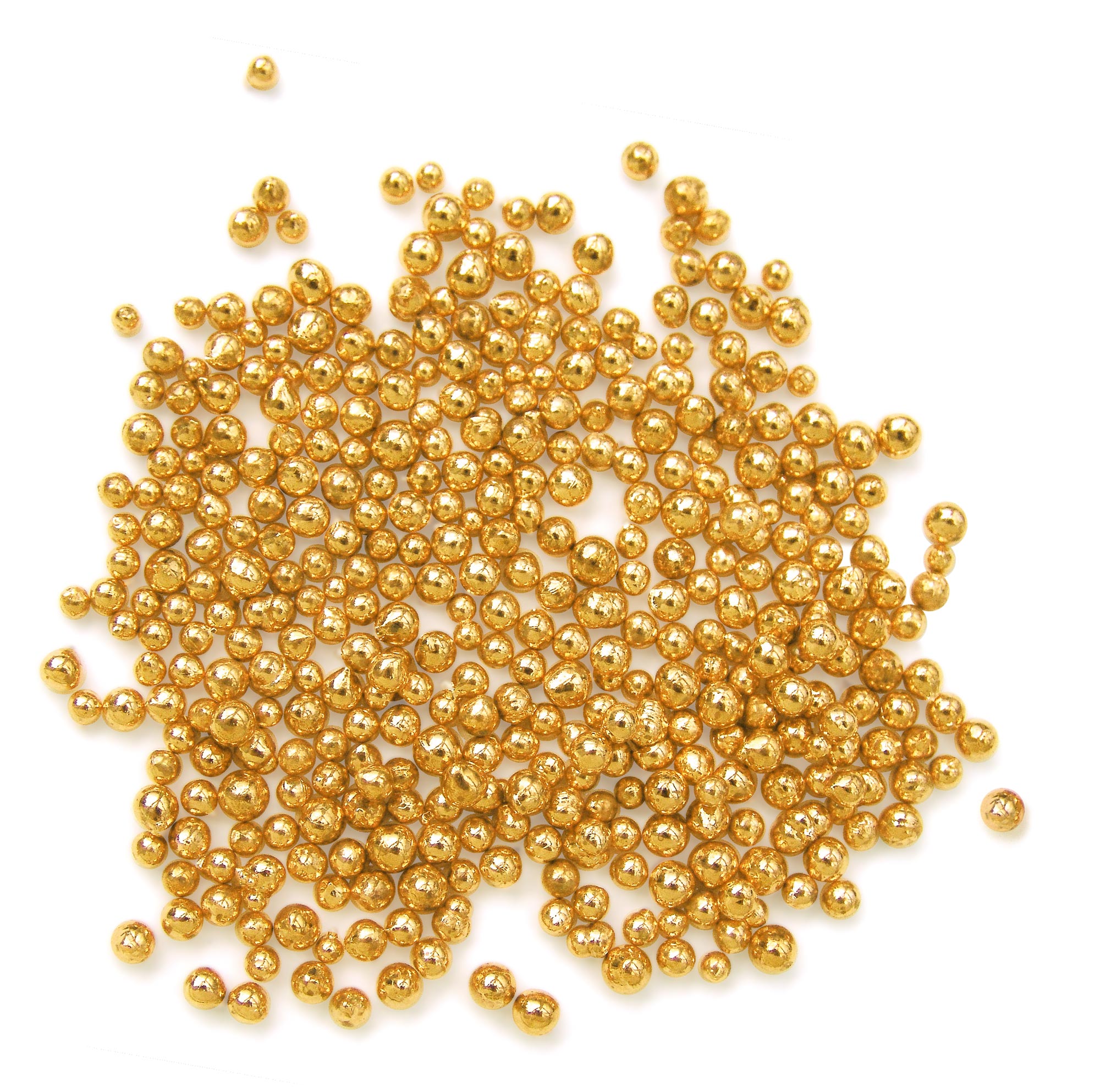
Produktion of Granules
with the easy to install granulation tank
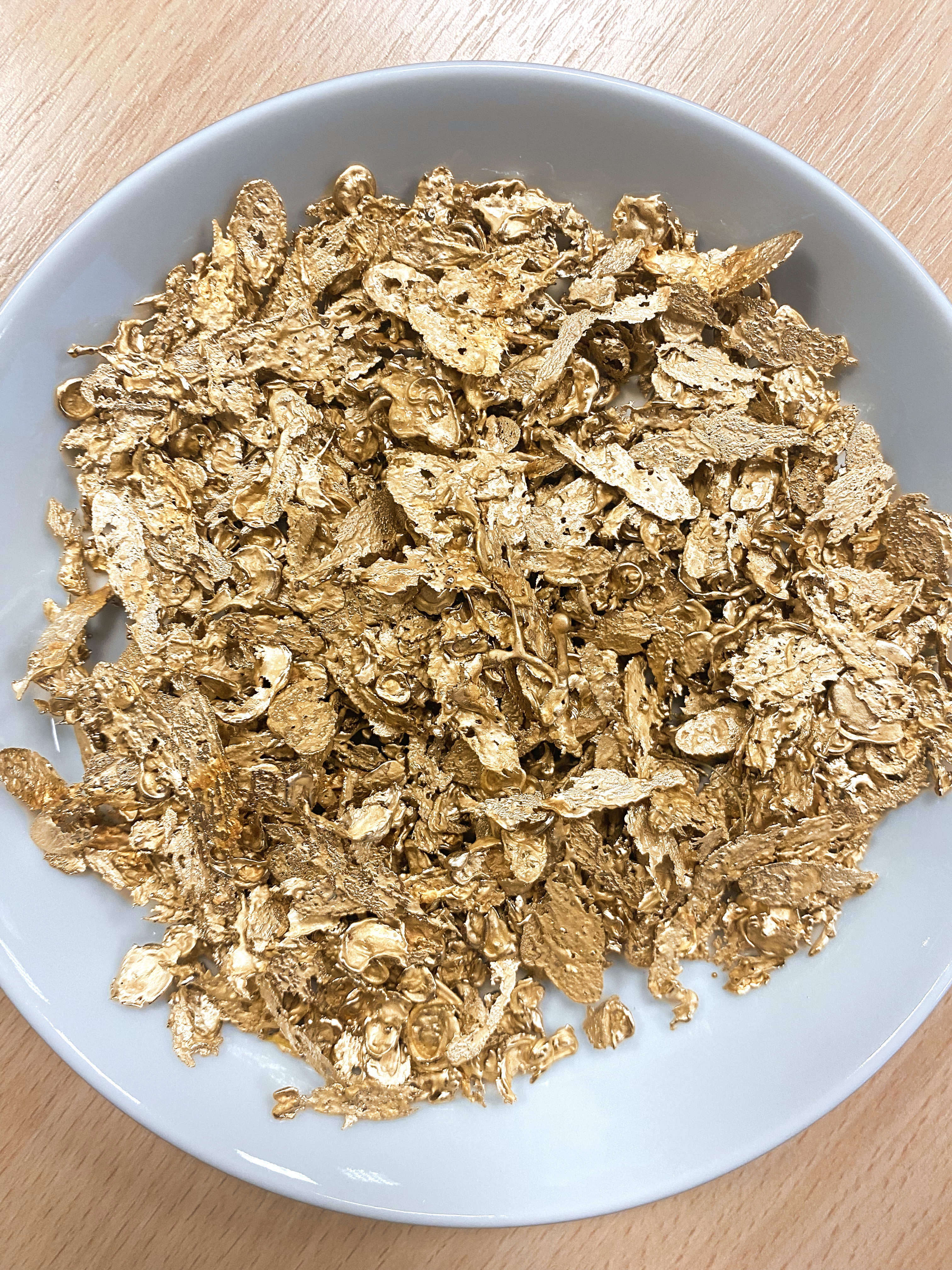
Produktion of Flakes
for sintering/diffusion bonding or refining applications
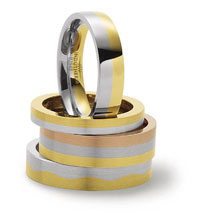
Produktion of Multi-Layer rings and Bracelets
with the optional sintering/diffusion bonding kit
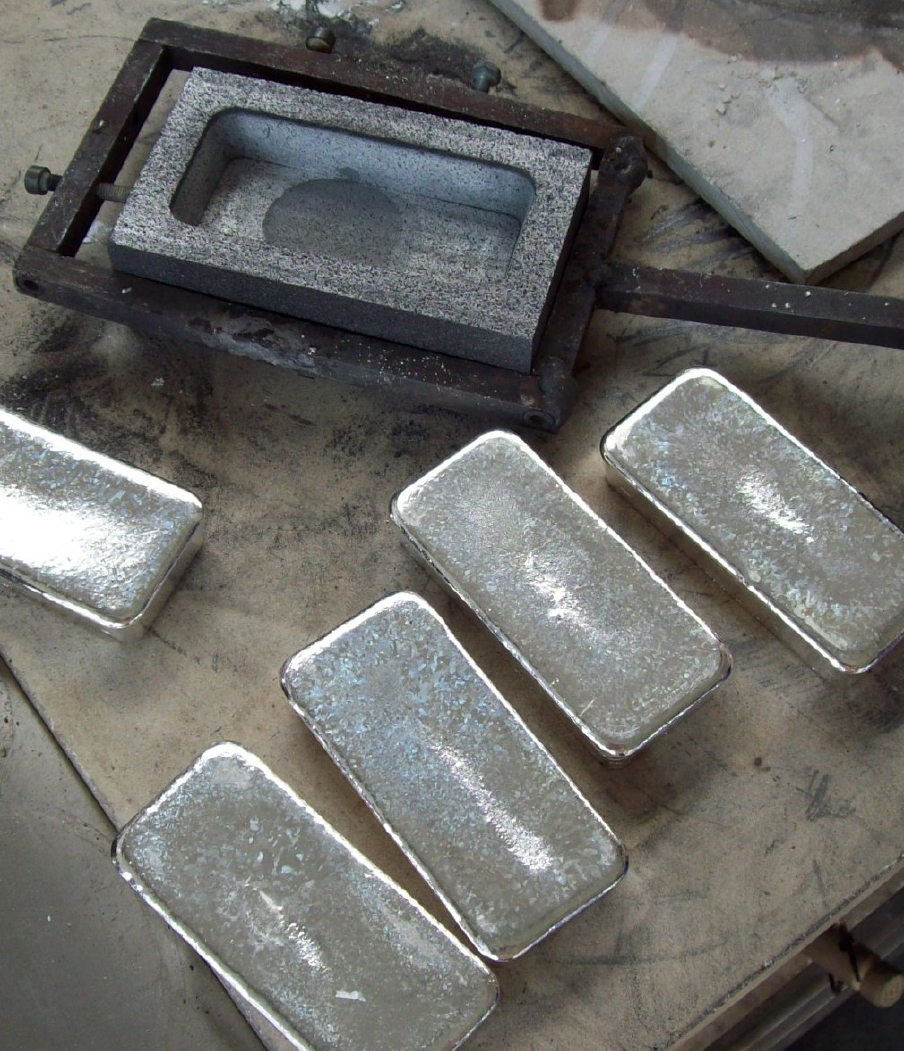
Casting into Ingot Molds
or any other molds
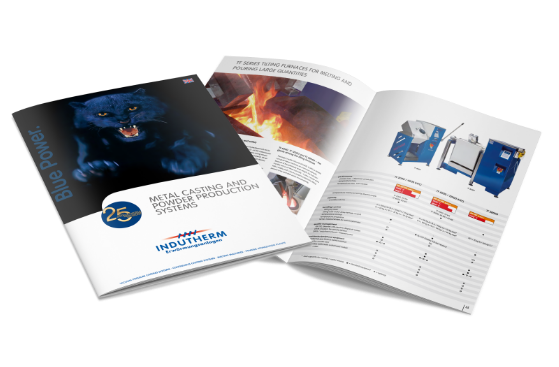