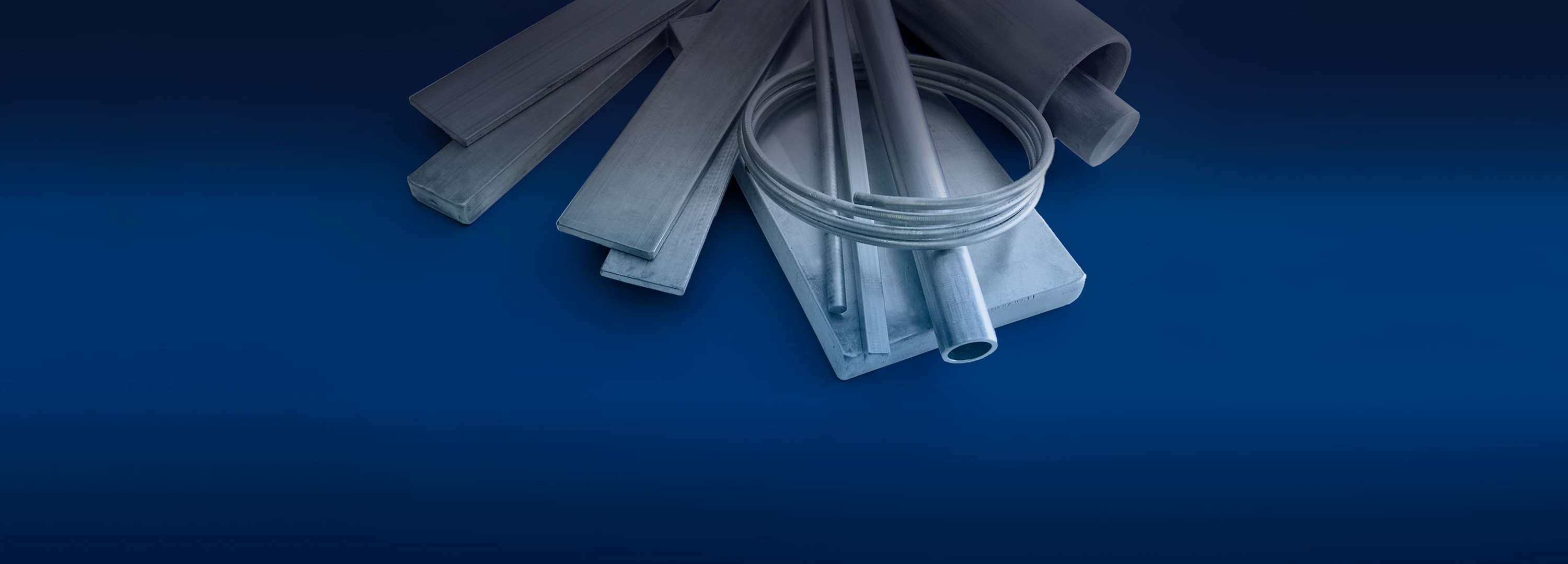
Zur Herstellung von Granalien kann man zwei Wege beschreiten:
- Für gelegentliches Granulieren lässt sich an einer bereits vorhandenen Indutherm-Gießanlage oder an einer Indutherm-Stranggießanlage ein Granulierfass einhängen.
- Wenn öfters oder permanent Granalien hergestellt werden sollen, empfiehlt sich die Anschaffung einer speziell zu diesem Zweck entwickelten Maschine des Typs GU.
Diese Maschinen wurden speziell zum Granulieren von Barren, Blech- und Gussmaterial in Granalien entwickelt. Die Granuliertanks lassen sich zum Entleeren sehr einfach entfernen. Erhältlich sind die GU-Maschinen mit Tiegelvolumen von 170 ccm bis 12000 ccm.
Haupteinsatzgebiete der GU-Maschinen sind das
- Herstellen von Legierungen aus Einzelkomponenten…
- Herstellen von Granalien zur Legierungsherstellung…
- Herstellen von Legierungen aus Feinsilber, Feingold plus Vorlegierung…
- Reinigen von schon einmal gegossenem Material…
- …jeweils unter Schutzgasatmosphäre oder Vakuum
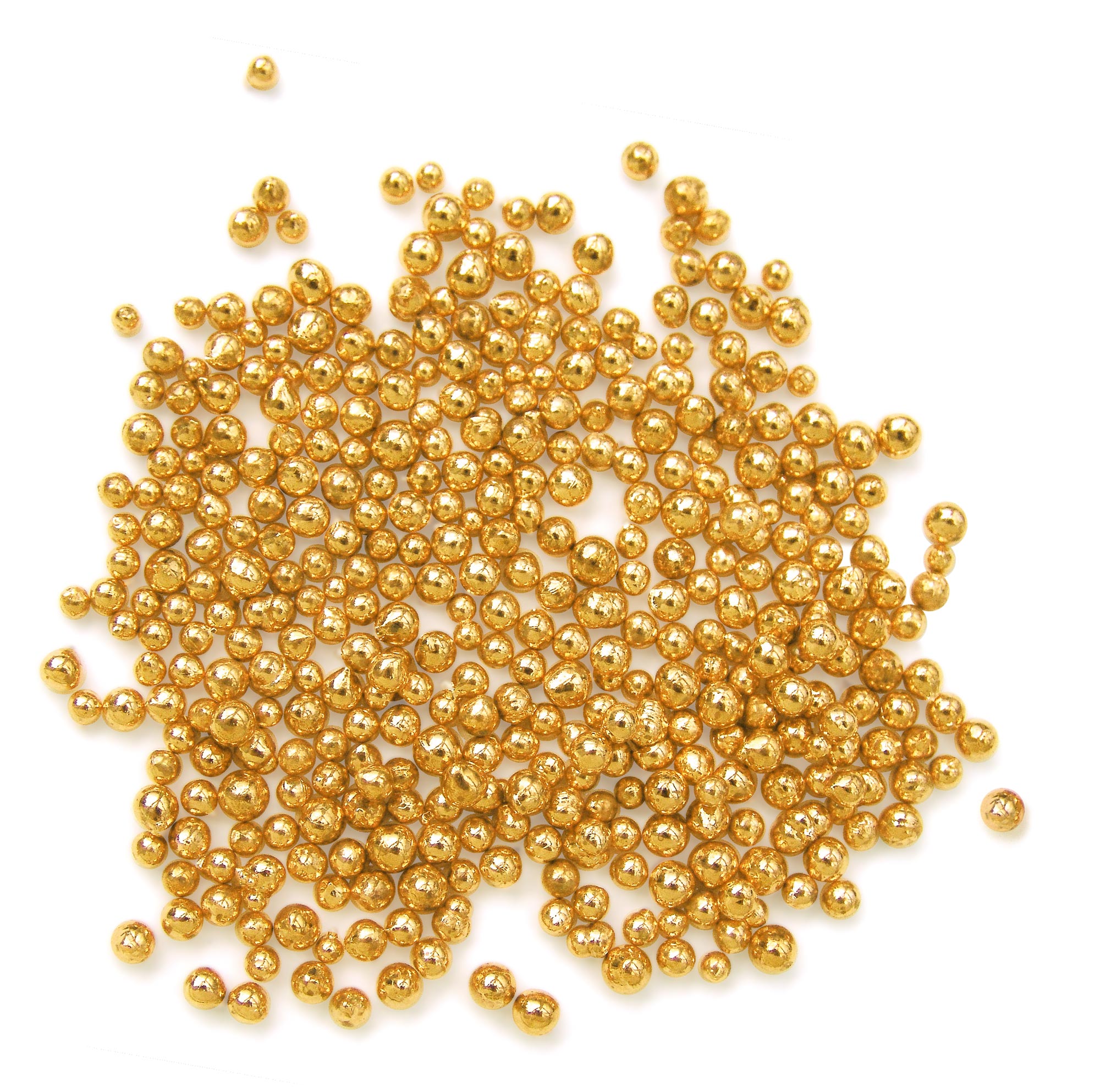
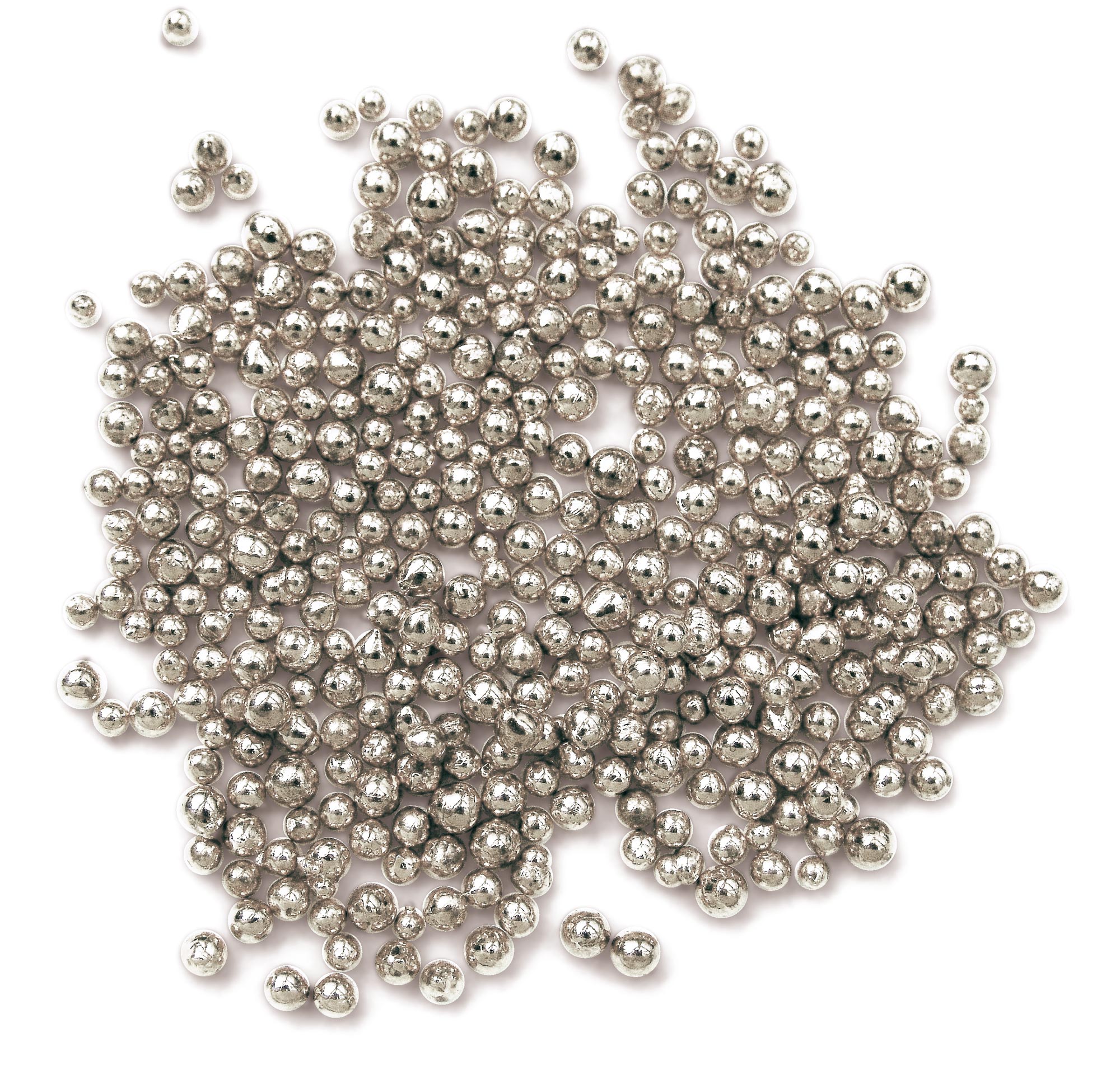
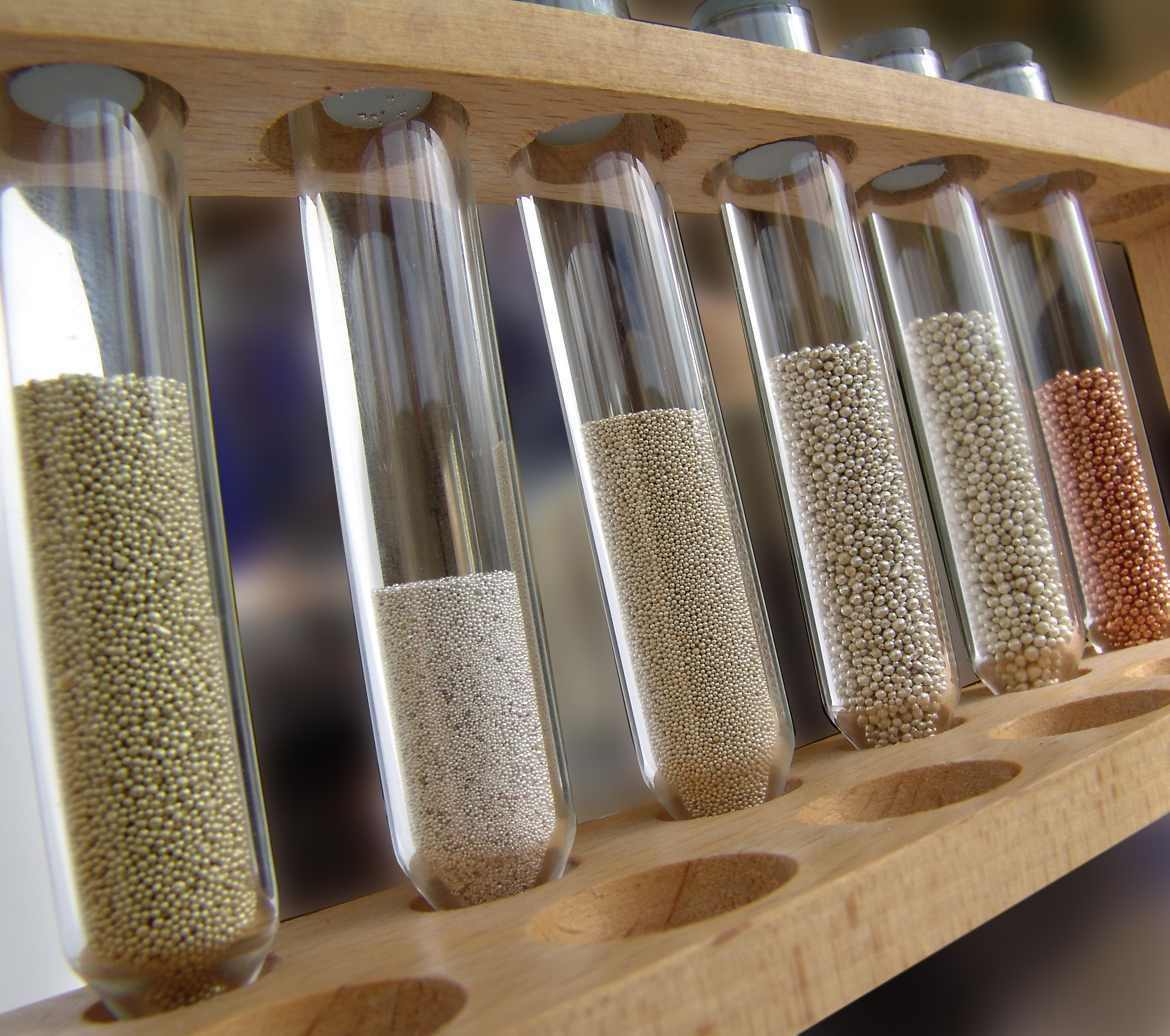
Daten im Überblick zur GU-Serie
■ Serienumfang, ○ Optional, - nicht verfügbarGU 500 | GU 500 HTC | GU 1000 | GU 1000 HTC | GU 3000 | GU 3000 HTC | GU 12000 | GU 12000 HTC | GU 25000 | |
Leistung
|
|||||||||
Temperatur max.*** | 1600° C | 2000° C | 1600° C | 2000° C | 1500° C | 2000° C | 1500° C | 1850° C | 1500° C |
Leistung max. / el. Anschluss | 10 kW (3x400 V) | 10 kW (3x400 V) | 20 kW (3x400 V) | 20 kW (3x400 V) | 30 kW (3x400 V) | 30 kW (3x400 V) | 40-60 kW (3x400 V) | 40-60 kW (3x400 V) | 40-60 kW (3x400 V) |
Kapazität
|
|||||||||
Tiegelvolumen | 0,245-0,386 | 0,4 | 1,5 | 1,7 | 3,4 | 3,9 | 12 | 14 | 25 |
Volumen in kg Au 18 ct | 3,6-5,7 | 3,6-5,7 | 22 | 22 | 51 | 51 | 180 | 180 | - |
Volumen in kg Stahl | 2,5 | 2,5 | 10 | 10 | 25 | 25 | 90 | 90 | - |
Volumen in kg Cu | 2,1-3,3 | 2,1-3,3 | 12 | 12 | 30 | 30 | 105 | 105 | 215 |
Volumen in kg Pt | 6,5 | 6,5 | 25 | 25 | 65 | 65 | - | - | - |
Volumen in kg Ag | 2,4-3,8 | 2,4-3,8 | 14 | 14 | 34 | 34 | 120 | 120 | 250 |
Die auf dieser Seite veröffentlichten Maschinenbeschreibungen und technischen Daten erheben keinen Anspruch auf Vollständigkeit. Sie können sich im Zuge der Weiterentwicklung ändern und sind deshalb keine Vertragsgrundlage.
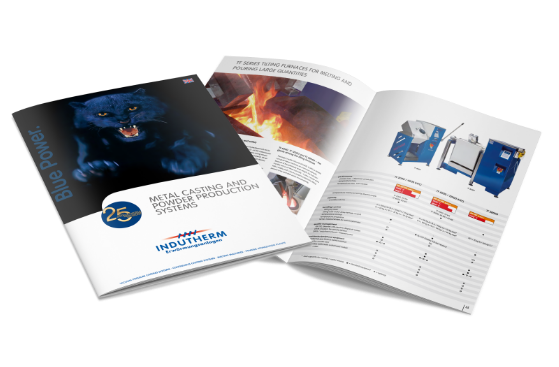
Sie möchten mehr erfahren?
In unserem Katalog erhalten Sie weitere Informationen